Optimizing Blast and Paint Processes in New Construction Shipbuilding
The efficacy of surface preparation and coating application in the new construction shipbuilding industry is fundamentally anchored in a well-coordinated, integrated approach. This intricate process, essential for achieving top-tier corrosion control, is methodically segmented into five crucial stages:
- Raw material entry
- Painting the modules
- Small parts
- Painting of erection joints at the module level
- Final paint and ship's completion.
Each stage is crucial in its own right but achieves its fullest potential when seamlessly integrated into an overarching process.
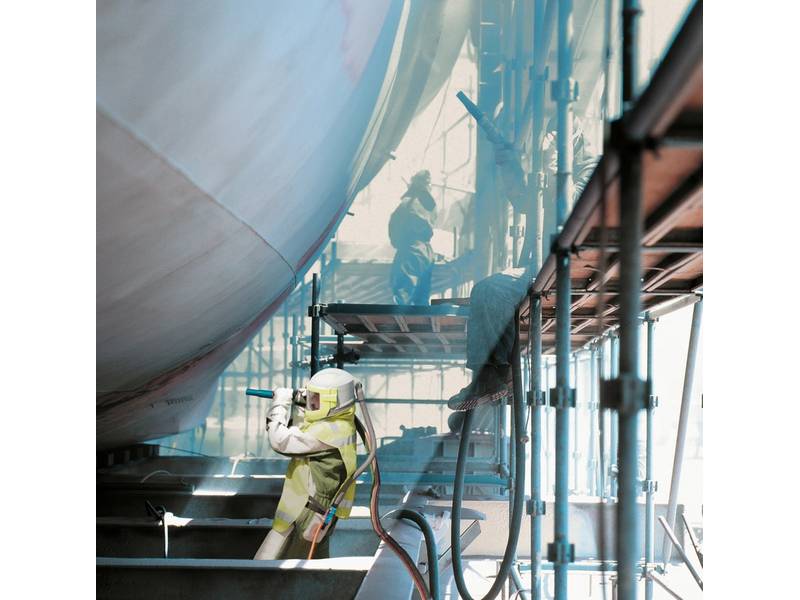
The shipyard: A symphony of collaboration
Imagine a shipyard as a football team, where the disparate execution of roles, along with precise timing and placement are paramount for a united victory. Just as different football teams leverage their unique strengths to create an advantage to win games, shipyards must employ unique strategies based on their resources and capabilities to efficiently complete vessels. The vast differences in facilities, such as pier space, crane capacities and outfitting areas underscores the necessity of a bespoke approach for maximizing efficiency in their respective blast and paint processes.
Navigating ship types and their unique challenges
The complexity within shipyards is magnified by the variety of vessels under construction, whether tankers or surface combatants, each presents its own set of intricate challenges. Tankers, for example, emphasize the throughput of steel and panel processing, while destroyers focus on electrical and mechanical systems, including combat systems. These differences highlight the importance of a nuanced understanding of each vessel type, enabling a more effective navigation through the five major paint categories and ensuring a tailored, efficient construction process.
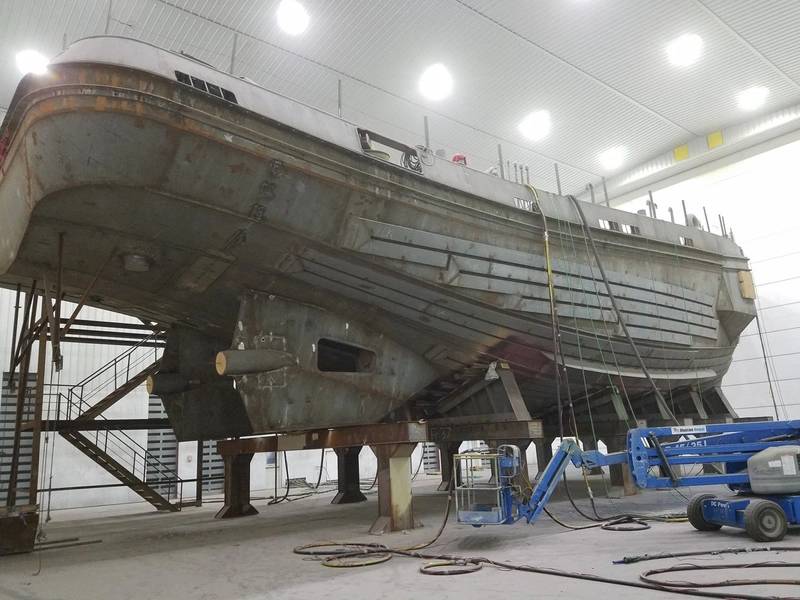
There are five major paint categories in new construction shipbuilding:
1. Raw material entry: The foundation
The initial stage of raw material entry sets the tone for the construction process. This stage poses critical questions: Should the steel be processed in-house with a wheel machine for primer application, or is it more efficient to source pre-primed steel? This decision significantly impacts the initial investment and operational costs versus the convenience and efficiency of using pre-primed steel. The choice between in-house processing and outsourcing affects not only cost, but also materials handling flow (and therefore efficiency) of the total construction timeline.
2. Module assembly and painting: A strategic approach
As the shipbuilding process advances, panels and bulkheads are assembled into modules, introducing a pivotal decision point regarding the treatment of weld seams and the timing of painting. The decision to paint modules before or after outfitting impacts throughput and requires careful coordination with the shipyard's spatial and equipment capabilities. Most Large Shipyards globally now have adopted a build strategy whereby the majority of the blast and paint occurs in module form. Large highly technologically advanced facilities now exist to efficiently blast, paint and cure modules. Without a well-considered blast and paint strategy that is aligned with the vessel's build strategy, timelines, efficiency and costs often become unmanageable and reinforce the age-old myth that blast and paint simply cannot conform to any consistently reliable engineered process. This is simply not true.
3. Addressing small parts: A key to efficiency
One of the most significant challenges in shipyards is managing small parts, which are prone to surface rust before installation. Optimizing the painting of these parts – through dedicated paint booths – can lead to significant efficiency gains and reduce the need for rework, showcasing the importance of thoughtful process-design in minimizing traditional bottlenecks. The efficiency of painting small parts in a dedicated small parts painting facility is often overlooked by Shipyard Facility Planners.
4. Erection joints and final hull coating: Optimize with technology
The painting of erection joints between modules and the final hull coating before launch are critical for both aesthetics and corrosion protection. Efficiently managing this stage requires a commitment to continued optimization of the blast and paint system, including updated equipment, abrasives, operator training and recovery methods. Proper planning, improving operator technology and incorporating automated system monitoring has proven to minimize both cost overruns and scheduling delays by effectively controlling the historically unruly wildcard of the blast and paint process.
5. Final paint: The finishing touch
The last stage, final paint, occurs post-launch and pre-delivery, offering an opportunity to employ advanced products and techniques such as foam blasting and paint touch-up kits. Research and innovation in this stage can significantly enhance efficiency and quality, highlighting the importance of staying abreast of the latest advancements in paint technology.
Conclusion
The optimization of blast and paint processes in new construction shipbuilding is a multifaceted endeavor that demands integrative systems planning, as well as adoption of new technologies and real-time monitoring processes that adapt to the unique challenges posed by each shipyard and vessel type. Contrary to popular experience and opinion, modern solutions do exist to the historically chaotic management of this critical path operation. By integrating the disparate five stages of the holistic process into an overall production strategy, shipyards can achieve unparalleled quality, efficiency and cost-effectiveness in their operations. This integrated approach not only enhances the performance and longevity of the vessels but also solidifies a shipbuilder's competitive edge in the dynamic maritime construction industry.
The author
Colin Gallagher, Director of Shipyard Optimization, BlastOne International