Maritime Design: Beating the Wooden Hull Drum
Even though there is still a substantial amount of wooden yacht construction and restoration out there, wooden hull construction has pretty much gone the way of the mastodonts.
To find a new commercial wooden vessel project would be quite a challenge. Except if you happen to know Scarano Boatworks.
Scarano Boats was founded by brothers John and Rick Scarano in 1986. They are located in an old waterfront fertilizer factory in Albany, New York and, too quietly, have built a variety of boats that boggles the mind. Their portfolio defies description. They have built USCG inspected passenger vessels, historic replicas, tiny experimental cruisers, private yachts, adventure schooners, head boat schooners, and billboard, hot tub, and solar hybrid electric drive catamarans.
Almost all the vessels built at Scarano were designed under the leadership of John Scarano. In an oversimplified description, John mostly runs the yard, while Rick mostly runs their boat operations under the name Classic Harbor Lines. Classic Harbor Lines runs about 12 USCG inspected sailing and power passenger vessel in New York City, Boston, Newport, RI, and Key West.
The vast majority of the Classic Harbor Line vessels were designed and built by Scarano boats. While some look similar, all are original designs where the oldest vessel (a wooden schooner) is about 30 years old. The newest vessel, a 114-foot passenger vessels that resembles a 1930’s New York City commuter is presently under construction in the yard.
The vessel presently under construction, I’ll call her Manhattan III, is an evolution of Manhattan I and Manhattan II which are earlier aluminum passenger vessels that have a similar retro appearance.
However, the new vessel is being built out of wood instead of aluminum, and John has a very good reason for it. It is less expensive to build, more fun to built, and will cost no more to maintain than an aluminum vessel. It will even be a little lighter than an equivalent aluminum hull.
John loves wood, but he is not sentimental about it. He simply knows that wood is better in this application and actually in many other boatbuilding applications. John and Rick know this because they design, build, and operate boats, which is a unique opportunity to look at the cost of boats over their entire operating life. To them a boat is a complete lifetime package. Not a sales pitch by a designer and a builder with a profit motive, to only pass the vessel to an Owner who will have to make the best out what he has been provided. Moreover, they are completely unafraid to stray from the beaten path and to experiment. Their experiments have run for over 30 years and the results are in.
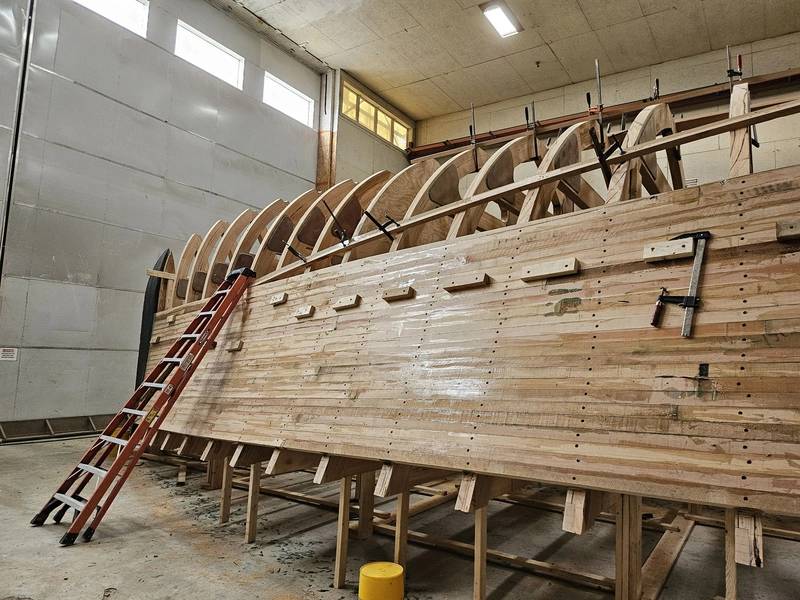
As long as custom wooden boats up to about 150 feet in length are properly designed and maintained, they are less expensive over their life than aluminum, steel or composite boats.
This may seem hard to believe, but let’s take a quick look at the construction of Manhattan III.
Manhattan III is a medium speed powerboat that will be carrying passengers in comfort and style.
She is douglas fir epoxy strip planked on laminated frames with multilayer plywood bulkheads. She will be covered on the exterior with about 36 ounces of glass and her interior will be sanded and painted without further composite laminating. It sounds conventional, but technology plays a significant part in the construction. Since the entire hull is 3D modeled, the frames are laminated to a rough shape on easily developed dimensions. Once cured, the rough frames are machined to exact dimensions on the NC mill. The frames are erected upside down, and from that point on strip planking can be performed in an incredibly straightforward process that is no more complicated than basic basket weaving.
John has built wooden boats with more complex approaches and also with simpler approaches (down to hard chine fiberglass covered plywood construction on boats that still pass USCG inspection 35 years later), but this approach is so straightforward that it actually begs for semi production line construction.
Scarano boats is a busy shop running many simultaneous projects, so it is difficult to put a large team on the strip planking job. While it is done within the budget with two ship carpenters who are making slow and steady progress, it would be much more fun, much faster, and even much cheaper, if it were done by a gang that spent some time optimizing the production line.
A team of six builders consisting of one skilled boat builder and 5 teenagers would probably be able to plank this boat at 50% fewer total manhours than John’s two skilled boat builders, who spend way too much time picking up and moving tools, moving staging and trimming fresh planks. Once the team would get the rhythm going, it would be a thing of beauty to behold, and construction speed would rival skilled laminating teams building hulls (and framing) in prefab molds.
This may seem counterintuitive, but remember, with composite molded hulls the job is not done until the frames and bulkheads are laminated in. However, on this strip planked boat the frames and bulkhead are already fitted when the hull is planked.
One may think the smooth molded composite surface is a time and cost saver (discounting the cost of the mold), but fairing this strip planked hull is really not that much work and neither is the downhand laminating of the exterior fiberglass skin. Actually, the big cost saver between the aluminum hull of the earlier boats and the wooden hull is the reduction in fairing costs on the wooden hull.
Once the boat is flipped, the interior is half finished and the biggest decision rests on whether the laminated frames and hull interior should be finished bright or painted.
Modern urethanes work incredibly well on the wooden substructure with the fiberglass skin. Repainting these hulls does not occur more frequently than on any other hull material and the interior finish of these hulls outlasts any other interior hull material. The oldest boats in the fleet have seen very little interior refinishing and often refinishing destroys the patina.
What is also remarkable and unexpected is that proper hull repairs are less expensive than composite, steel or aluminum hull repairs. Especially aluminum hull repairs are expensive, and one of the reasons that John has moved away from aluminum is that he does not have to worry about stray current corrosion in today’s electrical world.
Are there any secrets to this approach?
Yes, there are a few. First, only an experienced wooden boat designer should design wooden boats, because drainage and ventilation are of vital importance. It is not difficult to achieve, but it requires almost fanatic attention to detail. Modern boat operation today requires dry bilges and this actually makes wooden hulls more attractive, since a wooden boat with dry bilges will actually live forever.
And finally, there is one thing that cannot be designed away. No vessel should ever lack maintenance, but with wooden boats it is absolutely imperative that they receive timely maintenance. A composite boat stands a change when neglected for a while, but a wooden boat will simply die from neglect. Love a wooden boat and it will love you forever, whether as your personal yacht or as a USCG inspected commercial vessel.
For each column I write, MREN has agreed to make a small donation to an organization of my choice. For this column I choose Rocking the Boat, a great kids boatbuilding and messing in boats program in Hunt’s Point NYC.