Maritime Autonomy: The Reality
While merriam-webster.com is succinct in its definition of ‘autonomous’, ask 10 people in the maritime sector what ‘autonomous’ vessel means to them and the responses vary widely. Achieving autonomous, unmanned operations is not high, today, on the agenda of many (if any) shipowners. What does command their attention? Building ships that are increasingly ‘smart,’ with integrated, connected systems that take on additional decision-making processes while helping to reduce crew size (and cost), and ultimately helping to make ship operations safer and more efficient.
While there are certainly a number of studies and project focused on commercial vessels and unmanned operations, generally when talk turns to maritime and autonomy it is positioned as a step-change technology where onboard systems become increasingly connected, increasingly ‘smart’ and increasingly enabled to make decisions with little or no human intervention.
“Autonomy does not necessarily mean ‘unmanned’ … I can see where an autonomous ship can still be a manned ship” said Mikko Lepisto, Senior Vice President, Digital Solutions at ABB. “Saying that autonomous is only ‘unmanned’ is incorrect. I see an autonomous ship that can perform any function without human involvement, but the human role is one of supervising what the autonomous control system does. It can be manned or unmanned.”
Ketil O. Paulsen, Technology General Manager, KM Technology – Research & Innovation, with more than three decades of experience in various areas of technology development at Kongsberg Maritime AS, agrees. Today he evaluates new technologies to see if they fit into the portfolio of Kongsberg Maritime.
“We are developing functionality for ferries so that they can go from point A to point B and moor by themselves. But most of the ‘autonomy’ functions is supporting the crew onboard, not necessarily taking away the crew. It is making their operations safer and more efficient.” Kongsberg is invested in a number of collaborative partnerships and studies on autonomous marine operations, with the pinnacle being the YARA Birkeland, the world’s first fully electric and autonomous container ship, with zero emissions. (See related story on page 37).
Another leader in the field of autonomous ship development is Siemens, and according to David Grucza, Director, U.S. Marine, Siemens Government Technologies, Inc., Siemens’ view differs slightly. “Some have a ‘bridge centric’ view of autonomy. Our view of autonomy is rooted in the fact that we are a vessel infrastructure provider around electrification, digitalization and automation. We look at it from integrated power and electrical systems. We look at autonomy from the infrastructure perspective.”
While many of the companies leading the autonomous push in maritime are ‘Fortune 500’, there is a healthy dose too of young, innovative companies that move with enviable speed and force, such as Sea Machines, which in a very short time has been involved in some high profile trials, including with shipping behemoth Maersk.
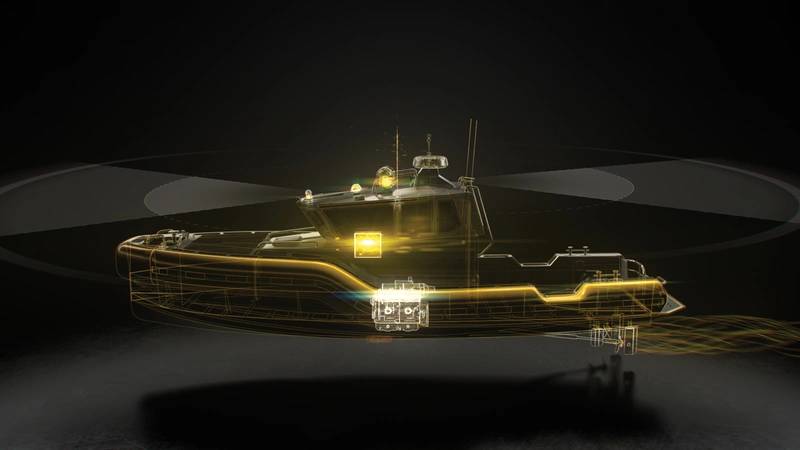
“Autonomy is advanced automation that manages compound missions with consideration of multiple streams of real-time variable feedback,” said Michael G. Johnson, Founder and CEO, Sea Machines. “As a comparative example, a traditional autopilot is considered simple automation, as it has very few if only one feedback signal to process – the actual course and heading versus set course and heading – and it aims to maintain the set heading without taking anything else into consideration, meaning that the human operator is required to manage perception duties of everything other than the heading. An autonomous auto-pilot is considered “more intelligent,” providing more value to the operation as it takes more information into account, such as position of vessel in relation to charted risks, traffic in the domain and it’s relation to the vessel’s intended course, or the potential need to temporarily slow or alter course in order to successfully complete the mission. The “autonomy” levels refer to the overall intelligence or capability of the system to enable the human operator to extract from direct control. We refer to our current autonomy product, the SM300, as a Level 3 system, meaning there is an active human operator in parts of the perception and emergency control loop.”
Looking at it from the perspective of class, Bjorn Johan Vartdal, Program Director of Maritime Research, DNV GL, is succinct. “Autonomous maritime operations is an operation controlled by an algorithm. A lot of people are mixing this with remote control and automation, but I think there is a distinction between that and autonomy.”
What’s Happing Now?
“It is moving fast, but people aren’t saying ‘hey, I need autonomy’,” said Grucza of Siemens. “They are taking the principles and applying them to newbuild designs. As people look at more robust and reliable power plants, which I think is a pre-cursor to autonomy, this naturally leads to adding energy storage systems onboard.”
One of the world’s largest shipowner/operators, NYK, is seemingly in step with this assessment.
“We are a shipping company, so to achieve an autonomous ship is not our objective: our goal is safer, energy efficient operations and more reliable logistics,” said Hideyuki Ando, Senior General Manager, Maritime Technology Division, Doctor of Engineering, Monohakobi Technology Institute (MTI) Co., Ltd., a research and development company which is 100% owned by Japanese shipping giant NYK. “Our goal is to be the most reliable cargo carrier. We see automation technology as supporting our objective.”
So where will we see autonomous ships develop first? General consensus points to local or regional routes due to fewer regulators and decision makers in play. “You will see local traffic – smaller ferries and tugs develop more quickly, because local regulators and operators can move much faster,” said ABB’s Lepisto, who’s company is involved in an innovative autonomy project on the remotely controlled ice-class passenger ferry Suomenlinna II (See story page 34). “There you will see commercial operations in a few years. The place where autonomy and autonomous technology will develop most quickly is in instances where there are ships with smaller crews onboard, where ‘autonomous’ systems are being utilized to increase safety and efficiency. Those ships will have the same technology as autonomous ships, but there will be humans onboard … it is a complimentary system to the captain and crew. This will move the fastest because there are not regulatory obstacles.”
Driving autonomy in all transport modes is the speed of technology evolution, a speed which is driving product and system obsolescence to a record pace.
“We would develop products that used to have an expected lifetime of maybe 15 years,” said Paulsen or Kongsberg, “but today we are looking at the time frame for new product to last maybe four or five years, and then it is being replaced by a new technology.”
Johnson of Sea Machines agrees. “OEMs that supply the industry are starting to announce the end of major analog and mechanical product lines that have served them for decades and the new technologies are being heavily marketed by leading legacy and young companies. In our look back at major transitions that are based on products that give significant returns on capital, it will take approximately 20 years for the “future ship” to be adopted by 70% of the industry. As example, readers should consider the time it took the unmanned engine room to be adopted by a majority of the industry,” said Johnson.
This speed of technology has, in turn, driven a corporate consolidation in maritime as the big companies grow bigger, and fostered an era of cooperation and partnership. “We used to develop most everything ourselves, what we do now are more partnerships with different companies and research institutes,” said Paulsen. And while technology is generally the center stage show-stopper, Paulsen argues that technology is not the main driver. “Years ago the drivers were technology; we are seeing now one of the main drivers is sustainability. Sustainability drives everything that we do today. It is all related to sustainability,” and it also is tied to autonomy.
What are the Next Steps?
While terms like “digitalization” and “big data” have arguably already become old hat in maritime circles, make no mistake that the increasing availability, seamless transfer and efficient utilization of data is the primary technical driver in the maritime industry today. “Ten years ago, most of the projects (at MTI) were about hardware – a better propeller, a bulbous bow, energy saving devices – that were discovered, tested and trialed at sea in a conventional fashion. Most projects at the time focused on energy conservation,” said Ando of MTI. “When we would run a (hardware) project about energy efficiency, for example, we realized that data is crucial to understanding the true performance of the vessel, now and in the future,” he said. With NYK’s fleet of 830 ships, the real ‘eye-opener’ came when the same technology was trialed on similar ships, and it was found that some ships literally consumed double the amount of fuel. “After we realized the importance of data, we (NYK) expanded the installation of data collection systems across the NYK fleet. We installed our own data collection boxes on our own ships, about 200 vessels.”
The original plan was to collect data in the name of improving energy efficiency, but “from 2012 we updated our system to also collect safety data as well as energy efficiency,” expanding the sensor data output from about 50 sensor data points originally to 1000 to 2000 data points today. “We collect all available data,” said Ando.
While data is the ‘blood’ of autonomy, it could be argued that power is the ‘heart.’
“What I see as a next step is an adoption of these technologies on manned ships,” said Lepisto of ABB. “On the development side there’s going to be an increased focus on the machinery side. Today there is a big focus on the navigational aspects, but there is less discussion on the machinery area, such as maintenance processes of the ships being changed to accommodate autonomy? There has to be a change toward a more electric power train to improve redundancy and reliability. Electric systems require less maintenance and are easier to build in redundancy.”
Grucza from Siemens agrees. “We look at the power and propulsion plant more holistically as a system. When you get to Autonomous vessels, I think that dynamic starts to change, too. For example, how much of the electrical load onboard a ship is for people and people support systems. That ratio for power for propulsion versus power for support systems is going to change. In a workboat today, most of the power is for propulsion, with some for crews & auxiliary systems. That ratio will change, with more for propulsion, the key technology is to view it systematically instead of just pieces and components. It’s about robust, it’s about reliable, and power and propulsion are at the heart of the matter.”
But according to DNV GL’s Vartdal, the electronics and sensor side – the navigation – has garnered the lion’s share of attention for a reason. “In terms of complexity, the navigation part is the most complex part to make autonomous because it requires situational awareness on a high level; It is a complex situation. With machinery functions it is much easier because there you can have a defined set of failure modes, whereas with navigation you have an infinite amount of possibilities. That’s what makes it most complex.”
“The next steps for Sea Machines are both continuous feature development on our existing products taken both from our roadmap and from customer feedback,” said Johnson. “We are also deep into the advancement of vessel perception technology, namely long-range machine vision which utilizes large data sets and A.I. to “see” and interpret the domain around an operating vessel by identifying, classifying, and tracking traffic and obstructions. This Sea Machines technology is currently being trialed aboard an A.P. Moller-Maersk container ship in the Baltic Sea.”
While the notion of ship traversing the waterways of the world yields some impressive artist renditions of the future, MTI’s Ando maintains that the process forward, fueled by huge amounts of reliable data, is anything but glamorous. “Not many owners/ship managers are at the level of fully leveraging the power of data,” he observed, adding “We believe in it, but it is a large effort to collect, clean up and effectively utilize data. It is a step-by-step, bottom up approach.”
What’s are the Challenges?
“Technically I don’t think it is such a big challenge,” said Ando of MTI. “I think the bigger challenge comes with regulation, insurance and liability, as well as social acceptance.”
Ultimately getting stakeholders moving in unison – from the owners and operators to the ports and logistics providers to the technology makers to the legislators to finance and insurance – is tantamount to moving maritime autonomy forward, too.
Grucza of Siemens agrees. “I still see regulatory and legal issues as the big constraint to go fully autonomous. I would assert that we are already seeing many stages of autonomy in the infrastructure today. I think it’s hard to get alignment on all of the different players in the chain,” (from ships to ports to logistics globally) … “that’s why you’re seeing some of the current developments being more regional focused, because quite simply you have fewer regulatory bodies that you need to get together and agree.”
“I think the main challenge is definitely on the market side,” said Lepisto of ABB. “The business case has to be in place for the operators to move toward unmanned ships or ships with less crews. As we discussed also, the regulatory needs to be in place, and that will start local and grow to national and international. With this, I also think there needs to be standardization within the industry in regards to collision avoidance” for example.
While most say that legal and financial issues will pose stumbling blocks, Johnson of Sea Machines cautions that the technology to advance autonomy in the maritime space, for the long haul, is not a trifling matter. “Building technology that safely manages multi-ton vessels in dynamic environments is not something to take lightly in any aspect of the development path,” said Johnson. “Our goal right now is to get enough SM200 and SM300 units into the hands of active operators because use in their worlds gives us feedback necessary to empower continued development.”
While Paulsen of Kongsberg also views regulation as the major hurdle, he points to a second challenge that must be thought through, too. “The second challenge is the mixing of manned vessels and unmanned vessels. For example in the automotive field, if all cars were autonomous and able to speak to each other, it would be fewer problems. As long as you have cars driven by people and autonomous cars, there are more problems.”
And while conversation and much debate swirl regarding the technology, the regulation, the machinery and the hull, MTI’s Ando sees the matter clearly and simply. “We can apply a fascinating technology, but if the crew does not understand (or use) the technology, it is useless. The captain, crew and ship management – all stakeholders – must be onboard for new technology upgrades for them to be effective.”
CASE STUDY: Suomenlinna II ABB & the remotely operated passenger ferry
A recent trial in Helsinki, Finland aimed to prove ‘the next step’ in autonomous shipping. The trial, with ABB and Helsinki City Transport, centered on a remotely controlled ice-class passenger ferry Suomenlinna II. In the remote trial, reportedly the world’s first for an existing passenger ferry, ABB successfully tested the enhancement of ship operations with technologies that are already available for nearly any kind of vessel. For the trial, Suomenlinna II was retrofitted with ABB’s new dynamic positioning system, ABB Ability Marine Pilot Control, and steered from a control center in Helsinki.Suomenlinna II normally voyages from Helsinki to Suomenlinna fortress, the UNESCO World Heritage site on a nearby island. For the remote piloting trial, the ferry departed from Helsinki’s market square, Kauppatori, and Captain Heinonen wirelessly operated Suomenlinna II with ABB Ability Marine Pilot Control through a pre-selected area of Helsinki harbor.
The trial took place during the vessel’s off hours, away from shore with no passengers aboard, in an area free of other vessels. While it is now equipped with the new dynamic positioning system, the vessel will continue to operate via a set of conventional onboard controls, with the remote mode deployed during the trial only. Research and development will continue with the ferry and her crew.
Suomenlinna II, originally built in 2004, is fitted with ABB’s icebreaking Azipod electric propulsion system. Additionally, the ferry was retrofitted with ABB Ability Marine Pilot Vision situational awareness solution in 2017.
CASE STUDY: YARA Birkeland
“The most exciting project today is YARA Birkeland; it will be the first unmanned autonomous vessel that we are going to deliver,” said Paulsen of Kongsberg. To achieve that there is still much testing, risk analysis that will lead to making the project a reality. YARA Birkeland will be the world’s first fully electric and autonomous container ship, with zero emissions. Kongsberg is responsible for development and delivery of all key enabling technologies including the sensors and integration required for remote and autonomous ship operations, in addition to the electric drive, battery and propulsion control systems. The design for the innovative ship was done by Marin Teknikk, finalized in 2017. The vessel is scheduled to be delivered from Vard Brevik in first quarter of 2020, and will gradually move from manned operation to fully autonomous operation by 2022.
Yara Birkeland Main particulars
Length x Width x Depth79.5 x 14.8 x 10.8 m
Draft (full/ballast): 6 m/3 m
Service speed: 6 knots
Max speed: 13 knots
Cargo capacity: 120 TEU
Deadweight: 3,200 mt
Propulsion system:Electric
Propellers: 2 Azimuth pods
Thrusters: 2 Tunnel thruster
Battery pack: 7 – 9 MWh