Marine News' Naval Architecture Roundtable
Marine News spoke to leaders at three North American naval architecture and marine engineering firms about some of the latest trends impacting their business today. Morgan Fanberg, CEO, Glosten; Robert Ekse, President, Elliott Bay Design Group; and Wade Carson, CEO, Vard Marine, weigh in on topics ranging from digitalization and decarbonization to the naval architect talent pool.
How are advances in digitalization and AI impacting the naval architecture business today? How will the role of digital technologies evolve going forward?
WC: Digitalization and artificial intelligence are fast becoming useful tools that will enable us to design and build more efficient, safer and environmentally friendly vessels. Vard Marine specializes in designing complex, tailored vessels that depend on the skill, innovation and experience of our naval architects and marine engineers. AI can supplement their capability by allowing us to more rapidly test and evaluate concepts, and to synthesize large data sets to provide increased options that will allow us to improve our products, but it can’t replace the blend of creativity and competence that allow us to solve the unique problems that our clients face out on the water. We have already seen the digitization of rule sets result in faster calculations, allowing the engineers to focus on improved design decisions rather than repetitive, manual tasks.
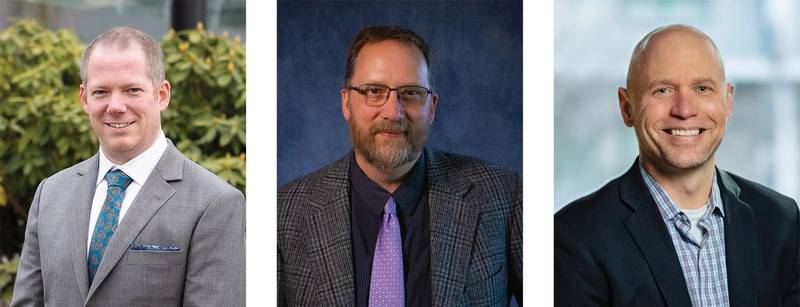
Moving forward, we expect to see dramatic improvements in the input data available to inform our decision making and thus the added value we are able to deliver to clients. Output from digital twins combined with data gathered from sensors on ships will allow better predictive maintenance and equipment selection, improve fuel efficiency, increase opportunities for vessel automation and provide deeper insight into vessel performance. As progressively more of this data becomes available, AI will allow the data to be synthesized into useful information that will guide requirements definition and design decision.
MF: Over 15 years ago, 3D scanning was a major technological breakthrough in retrofit work. Today, it has become as straightforward as using a tape measure and a camera during a ship check, similar to practices from 30 years ago. Since our first 3D scan in 2008, we have refined this process to the point where we can create detailed 3D models within hours of scanning, marking significant advancements in our modeling and simulation capabilities.
We have also made strides in automating other design processes. Simple structural designs can now be completed in minutes using our proprietary automation tools.
Advancements in monitoring vessel propulsion and auxiliary systems have led to significant improvements in predictive maintenance. Maintenance is increasingly based on trends and historical data rather than just run time, thanks to new data collection technologies.
These technological advancements are also driving increased automation onboard vessels, transforming how we operate and maintain ships.
RE: With all digital tech, we need to ask ourselves what it’s doing for us, specifically to the application that it’s being applied. Most of the time, these innovations are being driven by manufacturers. And they’re fully driven by the cost of manufacturing, meaning it’s more expensive to manufacture a knob than it is a button on a touch screen. You see this often in the automobile industry, where more and more functionality is being pushed into the information display, and it’s only because of customer pushback that newer cars come with a volume knob, for example.
These “technological advancements” are working their way into the marine industry as well—specifically, the wheelhouse controls, navigation, engine rooms, etc. Touch screens certainly have been a shift from solid state controls to digital interface systems that have multiple functions. If there’s an advantage to space-saving features or functionality that simply can’t be produced any other way, then I think it’s worthwhile to look at. We need to ask, “Why is this good for the owner? Why is this good for the platform?” We have a trade-off with tech, and that is system obsolescence and lack of the ability for the owner typically to do their own troubleshooting and maintenance. Those trade-offs need to be continually examined.
The maritime industry is seeing a growing uptake of vessel electrification and alternative fuel propulsion to drive down emissions. How is this affecting skillset requirements for naval architecture and marine engineering firms? Is it a challenge to add this sort of expertise in house?
MF: First and foremost, this push for electrification is creating a significant demand for marine electrical engineering. At Glosten, we recognized this growing demand years ago as propulsion systems were beginning to become more complex with advancements in diesel-electric and hybrid-electric plants. Our entire marine engineering team is trained in basic electrical design and now we are fortunate to have five licensed professional electrical engineers on staff.
Since we do not have the luxury of a crystal ball on how alternative fuels will be adopted, we must be able to design vessels utilizing all proposed alternative fuels. This requires significant internal technical and regulatory training to pass along knowledge to all of our marine engineers and naval architects. Much of this work contributed to our MARAD guide.
Most of this talent and knowledge growth has been internal at Glosten, led by our seasoned group of principals while also gathering intel from clients and operators who have better firsthand knowledge of these fuels.
In response to the increased complexity of electrical systems including all-electric and hybrid systems, the level of system integration engineering is increasing. These systems require equipment from various manufacturers, so to ensure everything works well together, naval architects and marine engineers must look under every stone and diligently review and engineer systems that will work or find solutions to these gaps.
RE: It’s more of an evolution than a shift. Naval architecture, mechanical engineering, electrical engineering, they have to interface with the manufacturer and regulatory bodies in a different way. How do you review a manufacturing system that encompasses what usually took several elements to put together to create a system? It’s all in one black box. How can that black box be integrated into the rest of the ship?
You have to communicate, you have to be able to speak to those details, to the purpose of the desired functionality and the requirements of the design with the manufacturers. In the days gone by, there used to be a fairly straightforward mechanical cut sheet that could answer the questions. This is the output of the pump, this is the horsepower that the engine is providing, this is the torque curve, etc. Nowadays, there is a lot of proprietary information included in that black box, that is created by the manufacturer that the engineer needs to be able to interface through communication to make sure that the output is going to be in conformance with the design requirements. Those soft skills versus simply the hard skills are what we really need to bridge the gap to cover that change in our processes.
WC: A strong holistic knowledge of multiple disciplines and the ability to work closely with specialists in different disciplines have always been essential to good ship design; however, the increase of vessel electrification has substantially increased the focus on the electrical discipline. Vard Marine has created an internal electrical department to ensure that we have the necessary skill sets from concept design through to vessel delivery to support our clients.
Marine electrical engineering has been a challenge to add in house as, though there are some great engineers out there, it is a skillset that was relatively rare in North America. We have had to build much of the capability ourselves and rely on support from our parent company in Norway to ensure that the department is able to address the rapid innovation in this space.
How do you see the overall evolution of power/propulsion solutions in the marine business?
RE: While new technology is moving very quickly in other parts of the transportation industry, the marine industry typically moves very slowly. In over the road transportation, for example, a truck may have a 10-year lifespan, while a ship, large tug, ferry or workboat may have a 50- or 60-year lifespan. Because of that and the sheer numbers that we’re talking about when comparing the marine industry to other transportation industries, there are much fewer platforms to speak of. The evolution of the marine industry is going to move a lot slower than others. So even with this initial thrust, this initial interest of alternative fuels, there will be people that can capitalize on the funding availability and the real strong interest in lowering emissions in the marine market.
I think the evolution of those markets are going to take a while to really settle, and for the most part, will be driven by the more rapidly changing elements from the other industries. What is the magic bullet for reciprocating internal combustion engines? Is it methanol, hydrogen? Any number of fuels or energy transfer systems are going to be clearly defined in industries that are moving much faster just because of their nature, the attrition of those pieces of equipment. The marine industry has a unique opportunity to watch the other elements of industry, see how they rapidly cycle through the learning curve of what’s happening. And that will inform the marine industry, I think, much more intelligently for that much longer-term, 50-year lifespan investment that owners are looking at.
MF: We foresee an increase in all-electric/hybrid-electric propulsion plants due to technology advancements in battery power density and the adoption of dual fuel marine engines. We also expect more adoption of energy-efficient technologies such as foiling tech for ferries, air lubrication systems to reduce drag, and new waste heat recovery systems to increase overall plant efficiency.
WC: We continue to see increased adoption of hybrid and electric propulsion systems. Given that our design portfolio is filled with unique and complex vessels, we are used to seeing variety of different power and propulsion systems, but the future provides even more opportunities to improve the fit and optimization of systems to the specific operational conditions of the ship. These opportunities will allow us to reduce fuel consumption, reduce emissions and reduce capital and opex costs.
Another key trend is the exploration of alternative fuels. Liquefied natural gas (LNG) has gained traction as a cleaner alternative to traditional marine fuels and will continue to be a key fuel for the coming decade. We are staying up to date with other fuel sources and have developed concept vessels that both use and transport them, but infrastructure challenges and competition with other energy consumers will limit their uptake in the near term.
Many firms in the commercial maritime sector cite the attraction and retainment of qualified/talented staff among top challenges. What does the talent pool and job market for naval architecture/marine engineering look like? Are these challenges as present in your part of the industry?
MF: There’s absolutely a challenge with attracting top talent in the marine industry. We continue to see a widening gap in engineers with shipyard and construction experience. We can design amazing vessels that meet or exceed client expectations, but without staff that have construction experience, there’s an increased risk of overcomplicating designs that lead to cost overruns. We strive to simplify and design vessels with a construction mindset.
WC: The talent pool in our market has always been limited. We hire significantly from co-op placements and train our naval architects and marine engineers, providing them the opportunity to rapidly experience multiple projects across multiple ship types. The level of exposure that they receive, which is necessary to develop the experience they need, is difficult to find outside of a small pool of similar companies.
Due to the significant investment required to develop our skilled professionals, retention is very important to us. We prioritize continuous professional development, training, and opportunities to learn. We offer remote and hybrid working conditions, on-site opportunities at client shipyards, and placements at our parent company in Norway for knowledge transfer.
We have not experienced the same levels of turnover that have occurred in other areas of industry, but we have sought to improve flexibility and working conditions to attract and retain top talent.
RE: At Elliott Bay Design Group, we emphasize flexibility in our employment packages. We have a significant contingency of remote workforce. With that comes flexibility of not only where you live, but how you work. This seems to be a very high priority for younger people entering the workforce as well as some of the top candidates that are looking to write their own ticket for their future. I’m not necessarily talking specifically about remote work, but the flexibility that allows them to draw their own work-life balance. If people can create a system where that has the best chance of success, then I think firms have the opportunity to attract top tier talent.
I think the marine market for naval architects, marine engineers and electrical engineers has always been fairly small. The competition for that market is fairly tight. So, we’re all looking at the same resources to fit not only the hard skills, but then find those softer skills that we need, as we were talking about earlier, it’s a more well-rounded discipline that you’re looking for. Somebody that has that ability to pick up the phone and call a manufacturer or have a conversation with a client. That is really, really important. The number of available employees is not shrinking necessarily, but rather the specificity of what we’re looking for is narrowing. And on top of that, you have the market that emerged post-Covid, where people looking for work really had the luxury of many options. The job markets were simply in a condition to favor the employee, and that’s created some need for innovative business models to attract talent.
What do you see as the number one technology or innovation over the course of your career that has most impacted commercial marine operations?
WC: From a design perspective, I started my career at the tail end of the transition to CAD and I have watched the comparatively slow transition to an integrated 3D modeling environment. I had expected 3D modeling to move earlier into the design cycle much more rapidly, but until recently, the complexity of the systems limited their utility in the dynamic and rapidly changing environment of early-stage concept design, where prototype designs are the norm. We have relied on our own in-house developed tools, which we affectionately call 2 ½ D to bridge the gap.
For marine operations, the greatest impact has come from electrification and the integration of electronics. Greater control, more data collection, better communication, automation, better sensors for predictive maintenance have all resulted from this transition. These have also brought new challenges and the need for increased skills and knowledge from both designers and operators, but the overall benefit is clear.
MF: Adoption of automation. From simply opening and closing valves from a computer screen, to receiving real-time support and monitoring from equipment manufacturers around the world, these advancements have changed marine operations for the better. Soon the adoption of digital twins will allow us to simulate propulsion systems well before construction begins. We will have the opportunity to troubleshoot designs and greatly reduce the amount of commissioning time required after construction is complete.
RE: Mooring systems roles have had the greatest impact on the industries that I’ve been involved with. Mooring systems have come a long way since I entered the industry in the late ‘80s, early ‘90s. You have magnetic systems, suction systems, all of these quick, efficient and secure ways of mooring a ship, ferry or barge. You significantly reduce your tie-up time and increase the amount of time that you can spend moving freight, passengers, etc. from the platform to the shore or vice versa. That’s changed the way operators not only design their boats, but think about their operation, and has really changed the face of looking at turnaround time as a significant cost element to their operation. Before these systems were created, tying up a ship really was a formula that was kind of predictable and there wasn’t much magic to it. Everybody knew what this static way of thinking was, and advanced mooring systems changed all that.
A second element is controls. Station keeping and dynamic positioning coming from the oil and gas industry has created a part of the market that has advanced controls and propulsion systems. There’s been a resurgence of the cycloidal drive systems. Z-drive systems have really come into a stronger position, propulsion pods as well, not only with fuel economy, but matching the desired efficiency with the specific maneuverability that is required of the platform that you’re talking about. Those advances have really changed the face of the industry and created new dynamics for the owners to consider.
Where do you see greatest opportunities in the U.S. market currently? What is your firm doing to capitalize?
RE: I think the greatest opportunity is the modernization of the U.S. fleet. When you look around at the average age of river tugs, near coastal workboats or even ferries—although we have had a lot of money pumped into the ferry market in the U.S. over the last 30 years—the fleets are very old from an average age perspective. That’s an opportunity. There’s a lot of eyes on the cost of manufacturing, on stretching that dollar to capitalize the latest technology. There’s been some hesitancy without really knowing what regulations and technological advancements are going to come about. Nobody wants to buy something and then have that superseded by the next greatest solution. That’s why we see our aging fleet increase year over year. I believe we’re at a turning point. I think that operators are getting more confident about what they need, and there are funding sources out there that have allowed people to leverage their capital expenses into grants, etc. So that’s the opportunity I see. Whether it’s a midlife refit on an existing platform with a change of propulsion, maybe a slight design change on the hull form. With an aging fleet comes the necessity of renewal.
WC: On the commercial side, we are heavily involved in the transition to alternative fuels and the energy infrastructure market. This includes bunker vessels, wind farm vessels, the resurgence of the oil and gas market and power generation vessels. We are learning from the experience gained in European markets and tailoring them to suit the unique needs of U.S. shipyards and operators.
On the government side, the focus is on vessel automation. Removing sailors from harm’s way, allowing increased focus on mission execution rather than platform operation, and improving operational reliability are all key opportunities using innovations and improvements in technology.
MF: We’re seeing opportunities throughout all the sectors we serve in the maritime industry. Certainly, inflation and interest rates are delaying recapitalization projects, so there is (and always has been) a focus on keeping older vessels running whether due to aged equipment, steel corrosion issues, or, of course, keeping up with new regulations. We will continue to see an increase in alternative fuel and electrification projects. The space industry (pun intended) is really taking off.