Interview: Tim M. Clerc, VP Engineering, Seacor Marine
Tim Clerc’s maritime career spans half a century, starting with his cadet training in 1969 in the U.K. He sees hybrid technology as one of the most transformational technological developments in maritime in that span, and the company is currently awaiting its 10th hybrid, the Seacor Yangtze. Clerc discusses the hybrid strategy and offers some practical insights.
- If you had to pick one technology that you think has made the business of running ships more efficient, more cost effective, what would that be?
I think one of the most important technologies that I’ve seen in 50 plus years is hybrid, most importantly what hybrid can do with regards to reducing fuel consumption and reducing emissions load. I look back at some of the ships I sailed on as an engineering officer, and the improvements since then I couldn’t have even imagined 50 years ago. Also, particularly for offshore vessels, dynamic positioning (DP).
- Seacor is well-known, but can you give us a ‘by the numbers’ look at the organization today?
Seacor was founded by Charles Fabrikant in 1989, and over the years Seacor Holdings has encompassed many different business lines. Today, Seacor Marine Holdings is headed up by John Gellert, and we have in excess of 60 vessels. Importantly, the age profile of our fleet (about eight years old) is half the industry average. We’ve just came out of seven dreadful years for the OSV market and we, unlike the majority of our competitors, managed to keep our head above water. We didn’t reorganize, we didn’t go bankrupt, but it did give us an opportunity to right-size the fleet and really focus on that assets that matter.
During that time we brought nine hybrids to market, without the benefit of grants or subsidies; we had to do it ourselves. We started looking at hybrid technology back in 2013, and it took us another three years, but in true Seacor fashion, we have really gone for it.
Our fleet today is diverse, made up of PSV’s, both conventional and hybrid, fast support vessels, fast cats and premium lift boats. There have been a lot of ‘firsts’: we were the first to DP1 fast support vessel; we were the first with a DP2 fast support vessel, and importantly, we’re the first with a DP3 a fast support vessel. We have presence here in the US Gulf, Mexico, West Africa, the Persian Gulf, Central America and Guyana.
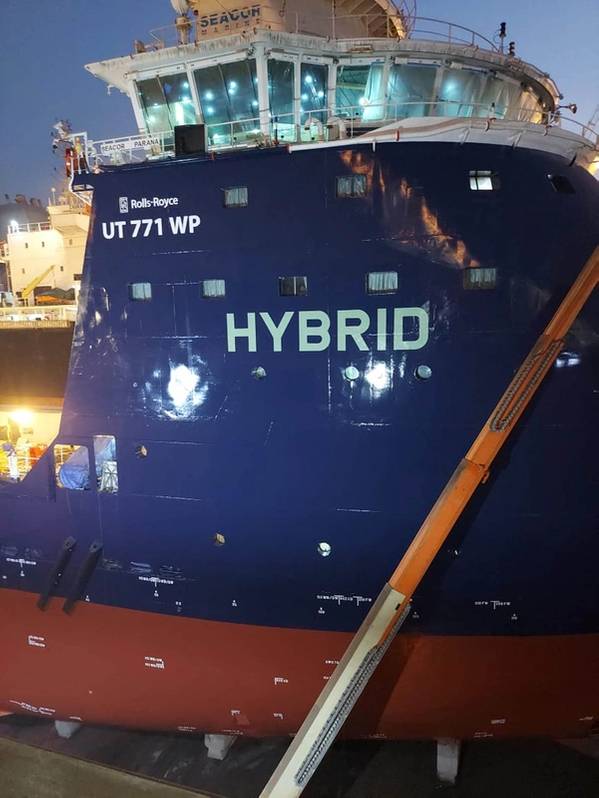
By permission of SEACOR Marine
- Can we look closer at the Seacor hybrid fleet, as you have number 10 in the works right now.I suspect you could hybridize anything if you had enough money, but what are the real benefits?
For us it’s hybridizing modern diesel electric [vessels, because] you are already halfway there, if not more. Those were the initial three target vessels. And then we were able to build on that with a series of seven vessels under construction in China, which we took over in the shipyard. Seacor Yangtze is the vessel currently under construction.
[In choosing to build new or convert to hybrid], you have to understand why you’re putting battery hybrid on board. Hybrid doesn’t necessarily have to mean batteries, although they do play an important part in most hybridization. But batteries, at the moment, make the most sense. At least it does to us.
- So tell us a bit more about the Seacor Yangtze.
The vessel was under construction at Cosco (Guangdong) Shipyard. She is a UT-771 CDL class, clean design length, diesel electric install. It has Caterpillar main engines, four 3512 engines, a full Rolls Royce package with alarms, automation, power management, energy management, and DP onboard. It’s a modern PSV and that was delivered around 2018. In total in China during that time we delivered five UT-771 CDLs both in Cosco Guangzhou and Cosco Zhoushan shipyards. We also delivered out of the yard six WP class UT-771’s, and we hybridized those in the yard prior to delivery. All of those boats came out and went immediately to charter where they remain, and we’ve operated hybrid vessels in the North Sea, the Mediterranean, West Africa and in Guyana. Importantly, we were the first to operate hybrid vessels in the Persian Gulf on a long-term fixture with Aramco. Some say it’s better to be second rather than first, but we were fortunate to have great partners in Kongsberg, Rolls Royce and ABS.
Tim M. Clerc, VP Engineering, Seacor Marine
- What’s your best advice to fellow shipowners that are considering hybrids: what are the challenges, what are the lessons learned?
What are the toughest things on a conversion like this? First and foremost, it’s having the funds available! There’s a lot of PSV’s out there that are crying out for such upgrades such as these [but as an industry, we need to get creative in finding ways to fund these conversions]. One thing that we’re looking at and hope to pioneer is an ‘energy as a service’ –leasing energy containers – which could help to get over the CapEx hurdle, to start.
The big thing with a PSV is space. We are not in the business of carrying fresh air around, so when those vessels come out of the yard, we have used every available space on board to fit our equipment and maximize cargo carrying capacity. Space is always going to be a challenge. A big one is space in the switchboard, as a lot of switchboards do not have available room for additional breakers. You end up adding additional switchboards, but then we need the additional space for those switchboards. It really comes down to fundamental project planning: writing a thorough spec; getting engaged with the designers and classification societies, being prepared to sit down and talk through the project with them.
And then good partnership with and supervision in the yard. Understanding that you’re going to have to have exhaustive trials once installed [to ensure the crew is well trained and prepared for contingencies, and to ensure that the system is operating as specified].
Best advice? Do your homework and understand why you want batteries on board your boat. What does it really help you do? How can they help you better support your customers? There is myriads of data available that people very rarely look at. When we started our first hybrid, we looked at 66 million recorded data points, and that’s just on power generation and power demand. In fact, we worked with DNV on a joint industry project regarding hybrid energy in the offshore domain. So we were able to look at that and then we could see what benefits could be gained from hybridization.
One last thing: hybrid systems are all about integration. Work with a trusted integrator, someone you have confidence in and someone that can talk you through it. We are by no means hybrid experts. We know a fair bit about them and we’ve been very successful in that respect. But always keep an open mind, always listen to other ideas. We don’t have the monopoly on good ideas. We believe we have quite a few good ones, but there’s a lot of smart people out there that want to be engaged in this technology. Keep an open mind.
By permission of SEACOR Marine
- You’ve mentioned batteries several times. Who do you use for your batteries?
I think hybrids really start with the batteries. We have had very good success working with Corvus for our batteries, particularly its Orca battery modules. Using the Lighthouse system, we can monitor our battery arrays and modules down to the cell level, looking at a cell and knowing exactly what the temperature should be.
For batteries, we look at a 10-year marine life. We check the state of health regularly and we can see on the graph if we’re operating the batteries too hard or too lightly? Also, we can’t forget the safety aspect of operating lithium-ion batters. Battery management systems, energy management systems have to be spot-on. Also, the design of the modules themselves, how each cell is protected from the other ones. We’re very happy with the service and innovation we get from Corvus.
As Seacor Marine works to complete the 10th hybrid vessel in its fleet, Tim Clerc, VP Engineering, Seacor Marine said in an interview with Maritime Reporter & Engineering News that “Hybrids really start with the batteries [and] we have had very good success working with Corvus for our batteries. In this video, we speak with Ole Jacob “OJ” Irgens, President and SVP Sales, Americas, Corvus, for insights on the Corvus battery and monitoring package, as well as updates on Corvus’ expanding manufacturing footprint in North America.
- We touched on this briefly, but from your experience, can you give insight on additional training needed for the seafarers to operate these hybrid systems?
It starts with the talent you have available. When we do one of these conversions, the crew are an integral part of it. They work very closely with the commissioning engineers when they’re out on trials, but we also run additional training modules, too. We’re stepping up that effort, as it’s been very difficult during COVID to move people around. That’s easing up now, but we’re also looking at [adding] virtual training [to the mix with hands-on training].
Also important is that interchange of knowledge and experience between the various vessels that operate hybrid. Thankfully the issues we’ve had have been mild. We’ve changed out the battery module, but probably the biggest issue with changing out battery modules is getting them to the vessel: we can’t fly them. Normally we keep some spares and we keep them charged to about 30% load so they can just slot in. The physical change out of a module is very easy. But training, especially from safety aspect of operating batteries, is important, and we believe that with the battery management system and energy management systems we have in place, the likelihood of a fault causing a problem is very slight.
By permission of SEACOR Marine