Interview: Chris Deegan, President & Chief Executive, Gibbs & Cox
In 1985, Chris Deegan was hired out of Penn State as a nuclear submarine cost estimator by the Naval Sea Systems Command and retired nearly 28 years later as the Executive Director of PEO Integrated Warfare Systems, with the last 10 as a member of the Senior Executive Service. He’s been with Gibbs & Cox since 2013, first as the Vice President of Engineering, and as President and Chief Executive since 2016.
Please give a “by the numbers” look at Gibbs & Cox today.
Since our founding in 1929, Gibbs & Cox has designed approximately 300 vessels including 24 classes of naval combatants, and nearly 7,000 vessels have been delivered to G&C designs. We proudly support military and commercial clients in the U.S. and internationally with all phases of marine design, construction, and lifecycle management. Our recent merger with Leidos Maritime Solutions positions Gibbs & Cox with well over 1,000 employees serving the maritime market.
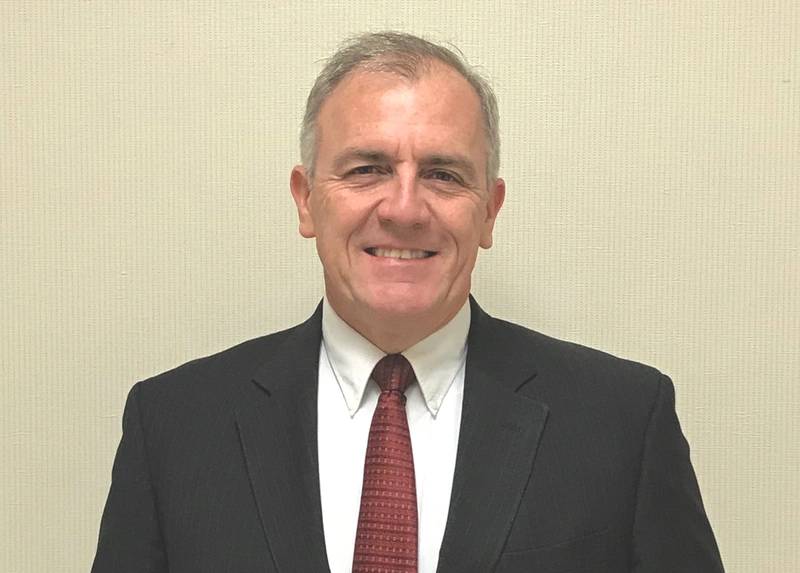
Which U.S. Navy shipbuilding projects Gibbs & Cox is involved in today?
We have a long and storied history of designing vessels for the U.S. Navy and government. The staff at Gibbs & Cox are experts in all stages of vessel design and sustainment, ranging from concept evaluation to detailed design and production engineering, and life-cycle support. Our knowledge and processes, honed with over 90 years of customer alignment, ensure that G&C designs meet customer requirements while being cost-effective and producible.
G&C delivers value to the U.S. government on the following ship classes: Freedom Variant Littoral Combatant Ship (LCS) Design Agent for Lockheed Martin, FFG-62 Constellation Class Agent for Fincantieri Marinette Marine, Medium Unmanned Surface Vehicle (MUSV) for L3 Harris, Large Unmanned Surface Vehicle (LUSV) prime, LPD 17 Flight 2 Program Office (PMS 317), Naval Sea Systems Command, U.S. Coast Guard and DARPA.
Internationally, we have interests in Australia, Canada, and several European and Asian countries.
Government shipbuilding projects—particularly naval projects—are some of the most challenging and complex.What do you see as some of today’s top challenges, and what do you count as the keys for success?
The loss of the U.S. ship- and boatbuilding industry to overseas providers has advanced foreign competitors’ skills, and provided entry to foreign competitors into the U.S. market.
Our success is wholly derived from our people and our emphasis on quality control. “First Pass Success” is what we strive for, and we have the skills and reputation to recruit the best. New employees have called us a “destination” employer—a place where they always aspired to work. That is a heck of a compliment in a very tight labor market amid a highly competitive ship design market. Our backlog enables our engineers and designers to experience a great variety of experiences. Our retention rate is far above all industry measures (97% in 2020). For decades we have advanced new digital shipbuilding tools to better integrate the multiple aspects of ship design. Looking back to the 1980s, we are able to do the same amount of design work with 10% of the staff that we needed to support the Arleigh Burke design.
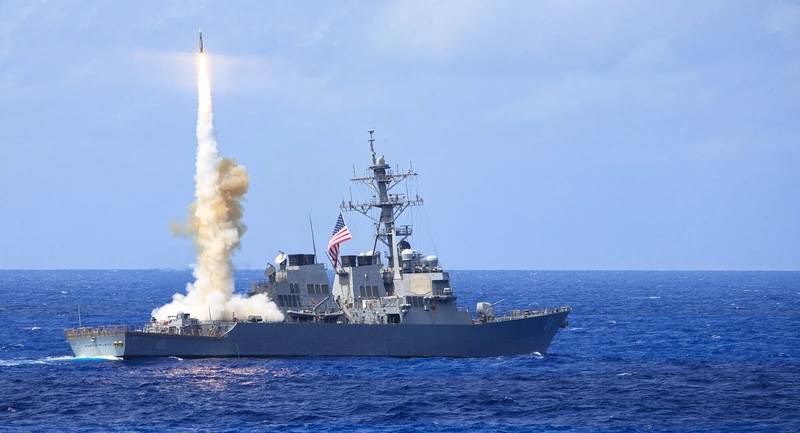
How do you balance the increasingly rapid evolution of technology found on navy ships with the fact that projects take many years to plan, contract, build and commission? How do you ensure the Navy is not commissioning ships with dated technology?
It may take a decade to design and build the first ship of a class. The key to keeping up with technological innovations is to work closely with the customer on their design requirements, and ensure careful consideration is provided for installing pier-side upgrades upon delivery and modernization through its life cycle.
Two key areas of innovation are Combat Systems and Hull, Mechanical & Electrical Systems (HM&E).
Combat Systems are heavily computer hardware and software based. Computer hardware is commercial product based, where technology evolves rapidly. Threats that the combat system encounter also evolve and are becoming increasingly complex. This presents an opportunity to counter evolving threats with improved computational power offered by evolving commercial market space.
Hull, Mechanical & Electrical Systems are generally the technology associated with basic hull, mechanical and electrical systems and do not change rapidly. One exception to this is the electric power demand, which typically increases as new combat system elements are developed and installed.
To ensure ships are not delivered with dated technology, two things are required: (1) Adaptable and flexible ship infrastructure that can readily accommodate just-in-time delivery of computer hardware, and (2) Acquisition programs that routinely and periodically refresh commercial computer hardware intensive systems and the combat systems software that runs them for in-service ships and provide the latest technology to ships as they are being delivered.
Looking specifically at the U.S. Navy, what are the key drivers for the “fleet of the future”?
For the foreseeable future, Navy ship designs will continue to pursue reduced crewing, parts commonality, modular architectures, and earlier consideration for modernization.
Last year, Gibbs & Cox was among several companies to win a design contract to develop a concept for the Navy’s Large Unmanned Surface Vessels. Will you walk us through this project and describe Gibbs & Cox’s approach to it?
The U.S. Navy is on a path to acquire several different types of Unmanned Surface Vehicles (USVs) as part of an effort to shift to a more distributed fleet architecture. This gets effective sensors, weapons, and other nodes out in number, while reducing costs and helping to keep sailors out of harm’s way.
The largest of the current USV acquisition programs is the Large Unmanned Surface Vessel (LUSV). The LUSV is envisioned by the Navy as an optionally manned warship, capable of fielding modular mission payloads that can consist of sensors, missiles, or other packages. It is expected to be up to 300 feet in length and weigh upwards of 2,000 tons.
Gibbs & Cox approached our LUSV concept design by initiating a thorough search of the military and commercial market to identify potential parent designs that fit the performance requirements of the LUSV while also emphasizing the critical USV enablers of reliability, survivability, and performance. We have an extensive library of ship characteristics feeding ship sizing tools that enable our team to rapidly identify platforms that are mission-matched to our client’s needs. Through this process we were able to select a parent ship design that offered an excellent foundation of warfighting capability aligned to the speed, range, payload, and other required characteristics of the LUSV program.
The military pedigree of the parent design offers an inherently survivable design, necessary to protect the crew when the vessel is in a manned status. When in an unmanned status, reliability is absolutely critical to mission success. G&C utilized our extensive experience gained from other USV programs to drive mission duration and reliability into the LUSV design through equipment and system redesign. This was fostered by our unique market position where G&C can integrate best applications from both military and commercial designs to tailor our LUSV offering. The end result of our efforts will result not only in a formidable USV design for the Navy’s consideration, but also a body of knowledge surveying the cost/capability trade space when finalizing the LUSV requirements for future acquisition phases.
Looking at vessel autonomy technologies, what are your thoughts on the pace and evolution? Specifically, where are we at on the gestation curve?
Looking at the autonomous car industry, there were lots of companies and pundits a decade ago that promised autonomous cars by 2020. And in the last few years, all of those companies have moved their predicted delivery dates far to the right (often by decades) as they’ve discovered the challenges of bringing autonomous vehicles to a consumer market.
The good news is that autonomous ships aren’t a consumer market. Many of the difficulties of driverless cars have to do with dealing with unpredictable people. Think about a four-way stop. There are rules about who goes when. How often do you see someone violate those rules? How often are you uncertain about whose turn it is next?
We have similar rules for ships, and while sometimes there are violations of those rules, and sometimes it can be difficult in the moment to know “whose turn” it is, those incidents are far rarer than with cars. The training required of professional mariners and the international rules governing maritime activity led to a high level of predictability. Machines are good at following rules, so when the people around them are consistently following the rules, it is easier for the machines to be autonomous. So, as long as we’re away from areas full of recreational boaters, ships do not have that very hard “people problem” that cars have.
One area that is more challenging for autonomy in ships is maintenance. The long periods of time that ships spend between ports dwarf those seen in other domains such as airplanes and cars. Ships generally require a lot of maintenance while underway, so in order for a ship to be completely autonomous, we will either have to design much more robust HM&E that can operate much longer without maintenance, or we have to design automated systems that can perform all of the traditional maintenance activities. At Gibbs and Cox, we are working on both of those approaches, but the solutions aren’t here today, and they are both likely to increase the capital cost of ships.
But there are intermediate steps we can take today. We can design ships where autonomy systems and human crew work together. Navigation and collision avoidance in fair weather are largely solved problems, and we can apply those technologies today to reduce the number of crew required and/or to allow the crew to focus on other tasks. Artificial-intelligence systems can improve the performance of human crews in other ways—machinery monitoring for instance. While building robotic systems to perform all the maintenance on a ship is still in the future, today we have automation systems that monitor machinery for faults in order to alert the human crew. These systems can also advise the human crew of the best course of action to take. We can use collaborative human-machine teaming approaches like this today to improve the safety and productivity of shipboard operations.
Related to “gestation curve,” Gartner, who might be considered one of the more knowledgeable prognosticators, said autonomous cars were “more than 10 years away” in 2010, “5-10 years away” in 2015 and “more than 10 years away” in 2020.
The real answer here isn’t end-date driven; it’s event driven. We’ve seen a lot of hype in the last couple years and industry activity beyond the first-generation disruptors and early adopters. The next step is to get real products in the water and begin to accumulate the data on what works well and what doesn’t so that we can pave the way the second- and third-generation solutions that will lead to genuine transformation of the maritime industry.
What does your firm bring to the table in the area of automation and autonomy?
Gibbs & Cox brings nearly a century of ship design experience, and familiarity with commercial and defense ship builders the world over, to the autonomy table. We’ve combined that with a new department dedicated to the design, development, test, and operational lifecycle support of unmanned systems. Our Autonomy department includes a number of industry specialists in robotics and other unmanned systems, as well as the industry partnerships they have developed over their own expansive careers. This department has racked up a formidable set of business captures, totaling a 200M$ portfolio that extends from concept development (DARPA SEATRAIN and NOMARS) through development and operations of a DOD program of record (Medium USV)—showcasing our systems engineering capability through the entire system development life cycle.
Gibbs & Cox is adept at preparing for and obtaining approval for American Bureau of Shipping (ABS) inspections for machinery control systems (MCS), including designing and programming/developing the hardware, instrumentation, and modular controllers required for orchestrating the operation of that machinery. We are commissioning a Controller Hardware in the Loop (CHIL) capability for the integration and test of various hardware, controllers, controller software and autonomy interfaces for future autonomous vessels. We offer solutions for the integration, evaluation, and test, including verification and validation, of multiple vendors for perception, avoidance and mission planning, classified data processing, and engineering operations control, all aligned to and supporting the Unmanned Maritime Autonomy Architecture (UMAA) development effort under the DOD.
Looking at the commercial maritime sector, what types of projects has Gibbs & Cox recently completed and/or is currently working on in?
G&C supports a wide range of customers in the commercial sector, primarily from our offices in New Orleans and Chesapeake. Our client base ranges from commercial marine operators to recreational boat builders. Our recent projects include supporting Norfolk Dredging Company with regulatory body compliance of their new 200-foot-long clamshell dredge. On the other end of the spectrum, our team recently developed a new product model for Cruisers Yachts, a fiberglass boat builder in Oconto, Wis. In addition to platform designs, we have clients in the development of mechanical systems designs. One project we are particularly excited about participating in is the modernization of the towing tank carriage for Virginia Tech. Our team is working with university researchers to upgrade the carriage mechanical and control systems and achieve a significant increase in system capabilities to facilitate hydrodynamic research which could not previously be conducted.
What will Leidos’ acquisition of Gibbs & Cox mean for the firm now and into the future?
For Gibbs & Cox, the transaction strengthens our capabilities by adding the technology-driven core of Leidos. It enables the leveraging of a wide range of technologies, including AI/ML, signal processing, sensing and rapid prototyping.
This Gibbs & Cox acquisition accelerates Leidos’ maritime strategy by providing placement, credentials, and capabilities to position for future U.S. Navy build plans. The renowned Gibbs & Cox brand, brings immediate credibility to Leidos maritime efforts and positions Leidos as a leading engineering design and autonomy provider for USV programs. For Leidos, this significantly up scales our naval architecture and engineering talent and prowess and adds production design engineers that can be leveraged across company.
The deal expands both companies deeper in the undersea domain through the combined marine engineering and platform integration capabilities.
The transaction will create a partnership between two companies driven by dedication to customer mission and will accelerate an expansion of products and services to current and future customers. Leidos intends to preserve and leverage Gibbs & Cox’s strong brand and reputation in the market. The intent is to keep the Gibbs & Cox business intact (including subsidiaries and joint ventures) and consider opportunities for adding in complementary capabilities from across Leidos. Gibbs & Cox will operate as a wholly owned subsidiary of Leidos.