GE Exhibits Latest Innovations at Sea Japan
At Sea Japan 2016, GE will showcase its latest marine technologies, helping Japanese shipyards and mariners achieve more efficient maritime operations while meeting stringent environmental regulations.
GE’s Marine Solutions business has been a reliable partner of the country’s marine industry. In the military space, Japanese Maritime Self-Defense Force (JMSDF) has chosen GE’s LM2500 and LM500 gas turbines for its naval ships. To date, GE’s marine systems’ supplier IHI has packaged, tested and delivered over 70 LM2500 and more than 30 LM500 marine gas turbines. IHI handles in-country design, manufacture and testing of GE’s LM2500 and LM500 propulsion modules for JMSDF programs.
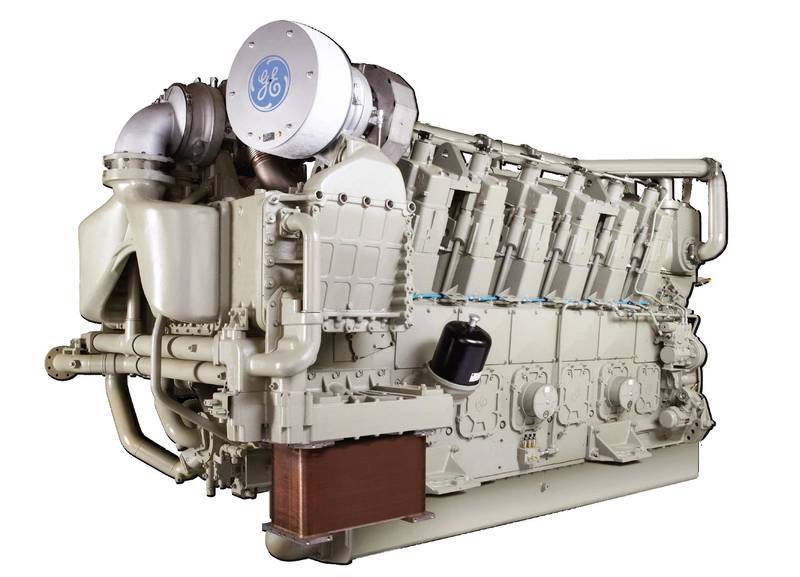
Japan is the global leader for LNG imports and has invested heavily in LNG carriers to meet its energy needs. GE has been selected by Kawasaki Heavy Industries, Ltd. to provide electric power and propulsion systems for two LNG carriers, adding to GE’s extensive global reference list.
COGES
By using GE’s combined gas turbine electric and steam (COGES) system, LNG carriers can meet IMO Tier III and U.S. Environmental Protection Agency (EPA) Tier 4 standards without the need for exhaust after treatment. The COGES system produces low emissions and can operate on either natural gas fuels or marine gas oil (MGO).
The team of GE and Hyundai Heavy Industries (HHI) received approval in principle from Lloyd’s Register (LR) for a 174,000-m3 LNG carrier to be powered by a COGES system. The COGES arrangement features a single LM2500, which produces 28 megawatts of power for propulsion as well as other ship service needs. The COGES LNG carrier will provide increased hull efficiency with the same cargo capacity in a smaller ship.
Separately, the GE/HHI/LR team also agreed to develop a gas turbine-powered, electrically driven, 14K containership design featuring a COGES system. The design will safely help to maximize the potential operational benefits of gas turbine systems. The 14,000 TEU class containership will provide a brand new vision for future container ships with enhanced operational efficiency and flexibility from the increased container intake and environmentally friendly dual-fuel system provided by the COGES system.
L250/V250 Marine Diesel Engine
GE’s L250/V250 Marine diesel engine reduces key emissions by more than 70 percent and is certified to meet IMO III and EPA Tier 4 emissions requirements. This in-engine emissions reduction technology eliminates the need for any urea-based selective catalytic reduction after-treatment system while maintaining world-class fuel efficiency and service intervals. The engine was first commissioned on Norway’s Bastø Fosen I ferry.
Most recently, GE’s 250MDC series engine with exhaust gas recirculation technology, which solely achieves IMO Tier3, has been shortlisted for the Marine Engines Award, demonstrating a remarkable step forward in engine technology innovation.
Electric Propulsion System
GE has developed a reliable and cost-efficient power and propulsion system combining induction-based technology with a pulse width modulation converter. In the last decade, GE has supplied more than 80 of these systems for LNG carriers.
Echogen
GE is the exclusive provider of Echogen Power Systems’ heat-to-power products to the marine market. This system uses carbon dioxide instead of water to convert the gas turbine or diesel engine exhaust heat to electricity. This achieves thermal efficiency of over 50 percent and reduction of weight and footprint of approximately 35 percent compared with steam systems. The compact, lightweight and economical product enhances all GE propulsion solutions, boosting system efficiency up to 50 percent.
SeaStream Insight
Powered by Predix, GE’s latest innovation in analytic software, SeaStream Insight, can predict potential failure of a part before it strikes. This predictivity will allow marine operators to make more informed decisions and provide the opportunity to help increase a vessel’s operational efficiency, driven by data. It will also enable a shift from planned to condition-based maintenance and can help to extend maintenance cycles.