Hydrographic Survey Vessel to be Converted for Unmanned Operations
A hydrographic survey vessel will operate in multiple areas of the Wadden Sea, commanded from shore by personnel in an office in Amersterdam.
U.S.-based Sea Machines Robotics, a developer of autonomous command and advanced perception systems, said Thursday that Dutch company Deep BV will equip one of its vessels with a Sea Machines SM300 autonomous control system to enable remote command of the vessel, including navigation and positioning, the control of on-board auxiliaries and sensors, and ship-to-shore data flow.
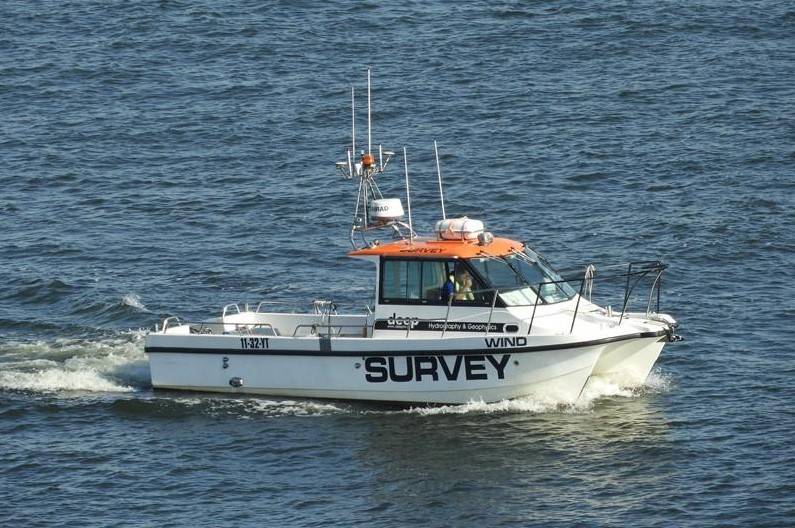
Sea Machiens says its SM300 autonomy system shifts full-mission vessel control effort from manual to autonomy system, enabling surveyors to remotely monitor and command multiple autonomous vessels from a shipboard or shore-based center located anywhere with network connectivity. This remote capability also reduces or removes high-risk activities generally associated with crew working aboard small survey craft in dynamic marine environments. By breaking the 1:1 crew-to-vessel relationship, companies can better utilize their technical experts across multiple concurrent projects, the company said.
In September 2019, Deep was the first company to conduct remote surveys without surveyors on board in The Netherlands. These early missions included a captain and crew on board, with surveyors based in the Survey Control Room executing data collections via the SIMON Remote Survey platform for marine survey data control and acquisition.
Now, Deep plans to initially deploy the Sea Machines-enabled vessel for a mission to survey the Wadden Sea, a challenging shallow body of water with tidal flats and wetlands located north of The Netherlands. With no surveyors on board the vessel for this project, Deep operators will command and control the autonomous vessel and all on-board payloads (including survey sonars, hydrophones, winches, cranes and davits) from its shoreside Survey Control Room, which has been equipped to facilitate several multi-beam surveys simultaneously. Deep will then transfer all collected data from the vessel to the control room via 4G and satellite connection. The combination of Sea Machines’ technology and the Survey Control Room will enable Deep to transition from minimally manned missions to unmanned missions in the near future.
“Sea Machines systems are an ideal fit for commercial marine operations that require high levels of predictability, productivity and safety,” said Sea Machines’ Michael G. Johnson, CEO. “For these reasons, hydrographic survey is an exemplary use case for our autonomous-command and remote-helm control technologies. With Sea Machines installed on board, Deep will benefit from obtaining higher-quality data, more safely and at a more efficient rate with less data overlap.”
“The purpose of our Survey Control Room is to offer our clients many possibilities like ad hoc surveys, simultaneous conducted surveys operated by only one survey crew, and multi-purpose use of vessels already available in the field,” said Deep’s Jurgen Beerens, CCO. “Besides these unparalleled flexibility advantages, it offers a time-saving option to increase efficiency and control costs towards a more sustainable future. With Sea Machines integrated on our vessel, we will soon begin to transfer tasks from the vessel to the safe working environment of the office. As well as improving safety, we will gain flexibility, continuity and quality, and we will reduce risks and our carbon footprint.”