HVAC: Three Challenges to Challenge Engineers
“On the 27th of July, 1850, I sailed from Baltimore in the ship Nonantum, of Boston, (Bates, master,) bound to San Francisco. In the ship's hold was stowed 1,050 tons of coal. The second morning after the commencement of the storm, smoke had been discovered between decks. The alarming truth instantly flashed upon our minds. The gas that originated from the coal had generated fire. They next proceeded to close the hatches, and caulked every seam tightly, in the hope of arresting the progress of the fire it was impossible to extinguish.” -Incidents On Land and Water, or Four Years On the Pacific Coast. D.B. Yates, Boston, J. French and Company, 1857.
Ever since open vessels were enclosed into compartments, ventilation has been a paramount concern, for passengers, crew and the existence of the ship itself.
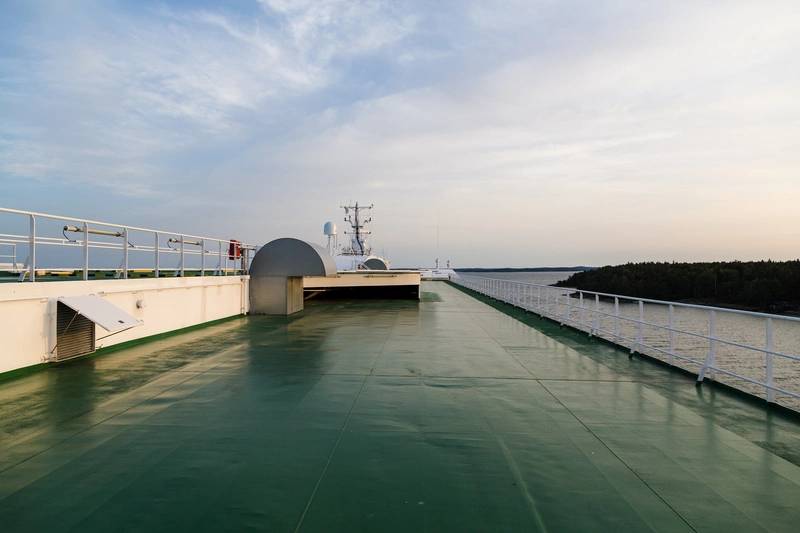
In 2021, and for the next few years, HVAC experts cite three top priority issues: the COVID-19 pandemic; energy efficiency; and finding safe, new refrigerants with low global warming potentials (GWP).
In some ways these challenges are linked. In other ways they are evolving separately. But each presents naval architects and ship owners with a myriad of questions.
I. COVID-19.
The cruise industry is at the eye of the COVID storm. Ventilation and air quality are central to the industry’s return to sail plans.
In July 2020, to tackle the pandemic crisis, the Royal Caribbean Group and Norwegian Cruise Line Holdings established a team of public health and medical experts, referred to as the Healthy Sail Panel. HVAC and ventilation were in the crosshairs. In September, in an extensive report, the panel recommended a number of HVAC and air management strategies. Examples include:
• Enhanced filtration – Upgrade HVAC filters to the highest level possible given the constraints of ship age and ventilation type.
• Optimize airflow patterns – Don’t recirculate air. If that’s unavoidable then use high-grade filters.
• Think strategically – establish preventative practices where the virus might be hardest to control or where crowding is common.
The report emphasizes that “HVAC upgrades can drastically improve filtration of pathogens” and that “cruise operators should make every possible effort to upgrade the HVAC filters throughout their ships to MERV 13 filters” (MERV = Minimum Efficiency Reporting Value, a 1 – 20 rating system in which 1 is the lowest level of filtration, 20 is highest).
The cruise industry, at least as represented by the Cruise Lines International Association (CLIA), supported the panel’s recommendations. “The CLIA Global Board unanimously voted to adopt all of the listed core elements for an initial restart of limited operations in the Americas,” CLIA wrote in a September 2020 press release. HVAC was among the listed core elements slated for change: “Ventilation. Air management and ventilation strategies to increase fresh air onboard and, where feasible, using enhanced filters and other technologies to mitigate risk.”
As the cruise industry works to get back to normal, it’s difficult to assess the extent to which the panel’s HVAC recommendations turned into actual shipboard projects. CLIA did not respond to inquiries about industry or membership metrics that might summarize recent investments in upgraded HVAC systems.
II. Saving energy, money and carbon
Vessel operators face worldwide pressure to decrease carbon emissions. That’s challenging enough. Now, add new strategies to control COVID-19. HVAC draws a lot of power. On a passenger ship, HVAC loads can consume as much energy as propulsion.
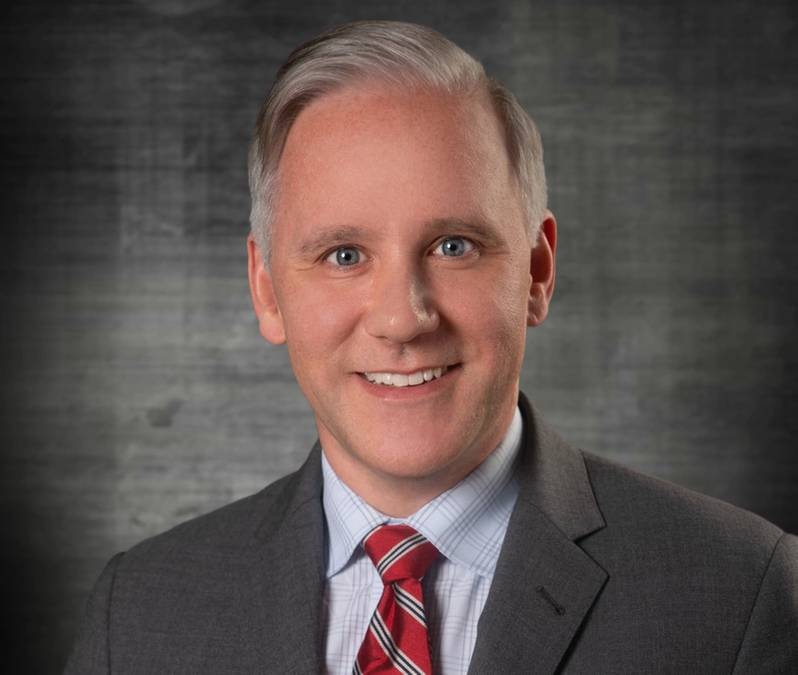
Kevin Glover, PE, is owner and managing principal at Coefficient Engineers, a North Carolina based HVAC-engineering firm; marine design is a core business segment. Glover also serves on ASHRAE’s HVAC Transportation Committee 9.3, which includes a maritime focus.
Glover explained how HVAC, COVID and energy are entangled. To start, consider that operating efficiency, across all of a vessel’s systems, not just propulsion, is a critical focus right now. Fuel costs are always a concern. And now, fuel consumption is a concern because of climate pressures.
Efforts to save fuel have been impacted by COVID-19, especially on passenger vessels. Research has shown that viruses are less viable within a narrow range of relative humidity (rh), 40-60%. Maintaining that range, however, in selective locations, presents numerous energy and engineering challenges.
The biggest energy demand on an HVAC system comes from removing moisture from fresh air. Standard practice, therefore, is to admit only minimal amounts of fresh air into a circulating system, thereby maintaining higher HVAC efficiency. Less moisture removal means less energy.
COVID introduced a new wrinkle. One of the most effective means to combat the virus is to dilute its numbers with large quantities of fresh air, and it turns out, the virus “dislikes” the same relative humidity range optimal for human comfort. This places new demands on ventilation and humidity control, Glover explains, even leading to “over-ventilating.” This provides healthier, more comfortable shipboard systems, he comments, “but the tradeoff is using more energy.”
Flagship Marine is a Florida based manufacturer of HVAC systems and components. Steve Brigham is Flagship’s Business Development Manager. He explains that on relatively small vessels, e.g., yachts, ventilation is straightforward: opening the hatches is usually sufficient. Larger vessels require make-up air units which draw outside air and treat it before the air is mixed within an onboard system.
Brigham said make-up units need to be properly sized so that fresh air, from just one pass across the evaporator or heating elements, closely matches the conditions aboard the vessel. Flagship uses copper to prevent the evaporators from being destroyed by maritime elements. In response to COVID-19, Flagship Marine offers U/V lighting with its air handlers and make-up air units.
Fuel costs and energy dynamics are leading HVAC designers to rethink fundamental approaches to maritime design. Kevin Glover described how these new approaches - from advanced 3-D modeling to digital twins – are expanding opportunities to construct energy efficient systems and still meet customer expectations. One idea: take the sophisticated building information modeling (BIM) used for land-based buildings and adapt it to vessel construction.”
“With 3-D modeling used for buildings, everybody on the development team has the same set of data,” Glover explained. Potential construction conflicts, say with electrical and plumbing, are resolved before construction starts. “This is applicable to marine design,” Glover commented.
More importantly, these models can account for the huge difference in designing HVAC for a vessel vs. a building, e.g., a building is static, its solar exposure is easy to track, and plan for. A ship’s solar exposure can vary by the hour. Ditto for ambient temperature and humidity and the full range of weather conditions.
“There are opportunities now,” Glover said, “to take advantage of new sensors, rich data, machine learning, and to tie all of this together into real-time operating abilities.” He said that in the past naval architects dealt with variable conditions by overdesigning multiple factors and building in redundancies.
Glover said 15-20 years ago there was resistance among ship owners about new tech and sensors and software. Now, though, raw material costs are going up, while tech costs have declined dramatically. “With a properly designed system,” Glover comments, “with real-time inputs about chillers, equipment, filtration, the whole turns out to be bigger than the sum of its parts.” Lower operating costs quicken payback times, not just in efficiency, but also in maintenance. High tech allows for real-time monitoring. And problems uncovered earlier are usually cheaper to fix.
III. Low GWP refrigerants
A third critical maritime HVAC challenge is linked to low global warming potential (low-GWP) refrigerants. Readers are likely aware that flammability concerns plague certain low-GWP refrigerants.
Brigham, with Flagship, commented that “the old reliable R22 is no longer being produced although it is still available.” He said that newer, proposed gases are environmentally friendly “but have some major concerns due to flammability.” This may not be a concern in well-ventilated shoreside applications. “However, it is a concern shipboard,” he advised, “where compressors are frequently located in tight spaces.”
Glover said that a large cruise ship, with heavy chillers, can safely use a low GWP compound that is not flammable. But for smaller cooling applications, even in relatively small quantities, high flammability is still a problem. Stateroom refrigerators are an example: each has very little refrigerant but there are thousands of such units. Glover said that because cruise ships are built in Europe, designers and engineers there have been somewhat ahead of this problem compared to their American counterparts.
Recently, though, low-GWP refrigerants moved to the forefront of America’s regulatory priorities. The new American Innovation and Manufacturing (AIM) Act passed last December requires the U.S. Environmental Protection Agency (EPA) to establish an allowance allocation and trading program for hydrofluorocarbons (HFC), the compounds used in modern refrigerants, called “potent greenhouse gases” by the EPA. By 2036, HFCs are to phase down to 15% of baseline levels. AIM is also supposed to facilitate “the transition to next-generation technologies that do not rely on HFCs,” according to the EPA.
This Phasedown started in May when EPA’s proposed rule was published in the Federal Register. While HFCs for some uses will get expanded allowances (e.g., military and fire-fighting) overall quantities will decrease.
The Phasedown raises almost endless questions. As HFCs become scarce, will the materials that remain available work in a maritime setting, just because they may work in land-based applications?
Glover said this is a top priority topic for ASHRAE. “We’re reviewing ASHRAE research and land-based developments of alternative refrigerants to determine the best way forward for maritime applications,” he said.
Stay tuned.