GLDD Preps for its New Hopper Dredge Galveston Island
With dredging business booming in the U.S., companies across the country invest in innovative new tonnage to get the job done more efficiently, effectively and safely. Chris Gunsten, SVP, Project Services & Fleet Engineering, Great Lakes Dredge & Dock (GLDD) and Patrick Webb, Senior Director Sales - Global Marine and Stationary, Wabtec discuss the tech inside the new Conrad-built trailing suction hopper dredge Galveston Island.
Conrad Shipyard recently launched Galveston Island, the first of two newbuild hopper dredges being built for Great Lakes Dredge & Dock Corporation. The new 6,500-cu.-yd.-capacity trailing suction hopper dredge is in the water and is scheduled to be in operation the first half of 2023.
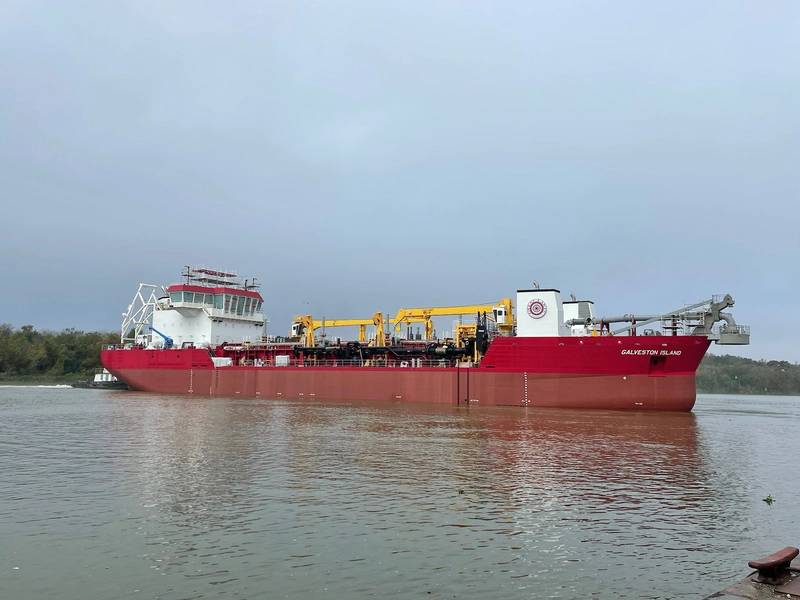
The dredge will be equipped with a direct high-power pump-ashore installation, dredging system automation, dynamic positioning and tracking, U.S. EPA Tier 4 compliant engines, and have capabilities of running on biofuel to minimize the environmental impact.
Great Lakes hopper fleet renewal program will be complete in 2025 with the delivery of the sister ship to the Galveston Island.
“GLDD is the largest provider of dredging services in the United States, notably among the first American companies to join the offshore wind industry with construction of our Jones Act compliant subsea rock installation vessel, which is expected to be delivered in early 2025,” said Gunston.
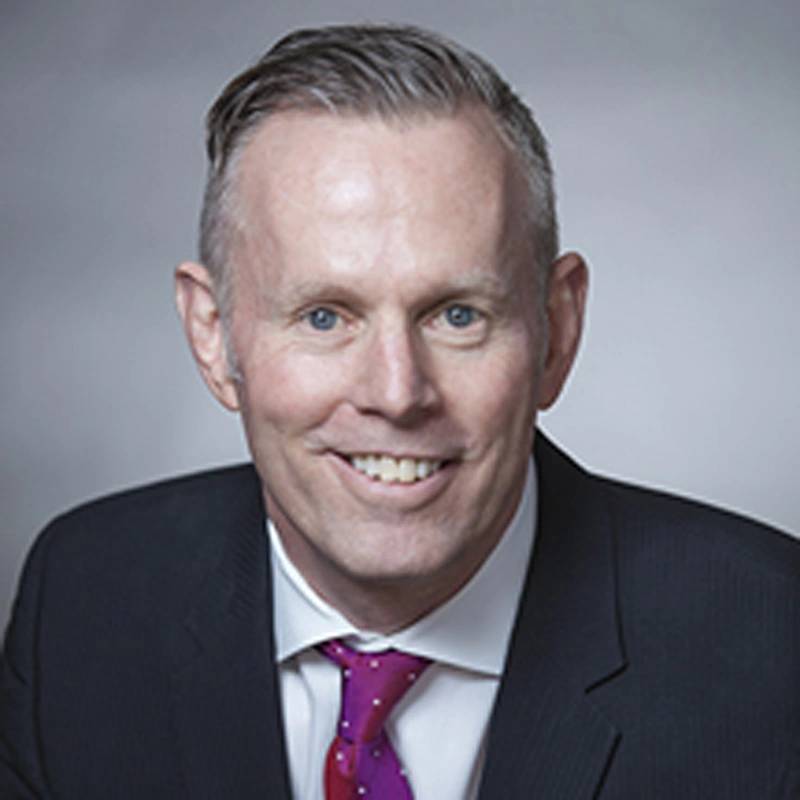
Chris Gunsten, SVP, Project Services & Fleet Engineering, GLDD
Image courtesy GLDD
GLDD has a long history of 130 plus years, with an equally long record of fleet investment and upgrade. “Currently we operate a fleet of 17 dredges that consists of five mechanical dredges, five cutter suction dredges, four hopper dredges, and then three smaller CSDs cutter suctions in our rivers and lakes division,” said Gunston. “In that mechanical division, we operate the largest backhoe dredge, dredge New York in the United States. That's also amongst one of the biggest in the world and several of the largest clamshell dredges in the U.S. market with buckets ranging up to 55 cubic yards; for context that's about six dump truck loads in one single bucket. Moving on to the cutter suctions, those are all 30-inch discharge dredges and range from 11,000 to 18,000 hp total installed.”
“Next up we've got our trailing suction hopper dredges (TSHDs), or just hopper dredges. These range in size from the small ones at 3,600 cubic yard hopper capacity, all the way up to 15,000 cubic yards, which is the dredge Ellis, currently the largest in operation in the US.”
GLDD’s most recent dredge to enter service was Mackey in 2017, but in looking at the fleet holistically GLDD operates vessels that date to the 1960s that have been continuously upgraded and overhauled to maintain efficiency.
In addition to the dredge fleet, GLDD owns and operates a wide variety of support vessels: scows, derrick's, launches and anchor barges.
“We're also really excited about is the construction of two purpose-built (Damen-designed) multi cat vessels. These are the first two being built in the US. They are quite popular in the international dredging fleets, but these are the first two that we're going to operate in the US and that's going to make a big improvement into the operability and the safety of our offshore operations,” said Gunsten.
Inside Galveston Island
GLDD’s new hopper dredge Galveston Island will soon be delivered by Conrad Shipyard, and predictably the GLDD team is eager to welcome the new technology and capability to its arsenal, particularly as the hoppers excel at working in offshore conditions, particularly suited for coastal restoration and beach nourishment. “One really important factor of that type of work is being close to shore to limit your pumping distances,” said Gunsten. “One of the best features of the Galveston is her relative shallow draft for her capacity. So that allows her to get closer to the beach, to be more efficient, and to use less energy to get the work done. She’s got the latest suite of dredge controls in automation, and over time, those automations will help the vessel remain as efficient as possible.”
Central to Galveston Island’s efficiency are its Wabtec EPA Tier 4 powerplants, engines that achieve performance without the need for urea.
“We wanted to get as efficient as possible without the need for the urea after treatments that are at costly and cumbersome to manage at times,” said Gunsten. “These engines also have the biofuel capacity. That's not widely available in a lot of markets [now] but they have that option.”
Patrick Webb, Senior Director Sales - Global Marine and Stationary, Wabtec
Image courtesy WabtecWabtec has a long and distinguished history building engines in Western Pennsylvania, a leader in railroad, stationary power, offshore energy and marine. According to Patrick Webb, Senior Director Sales - Global Marine and Stationary, Wabtec has invested about $700 million over the last 15 years in the EPA Tier 4 engines offered today, “and that engine is really the only engine in the marine industry that's been able to accomplish this very strict emission output without the need for any after treatment.”
The removal of aftertreatment, according to Webb, makes the system smaller and simpler for the customer the cost and maintenance of extra equipment, as well as urea which is a consumable. “So we reduce that cost, that operation complexity and make it much simpler to operate with a plug-and-play medium speed 900 RPM engine system,” said Webb.
In designing and building the engines that will power both of GLDDs new hopper dredges, Webb said compatibility in space and ease of use were central themes.
“We've tried to make build and design this engine to fit in a lot of our competitor's footprints from the last 50 years of legacy engines,” said Webb. “So that makes it easy for designers and operators to have a very simple setup.” In emphasizing the importance of “no urea”, Webb noted that some of the urea tanks can range up to 10,000 gallons, compounded by a USCG requirement for crawl spaces around the tanks in the event of a leak. “[Urea tanks are] big structures that are very expensive to build; that goes away with the Wabtec Tier 4. We don't have those tanks, so designers can use that space for carrying capacity. If it's a hopper dredge, they can have larger hoppers. If it's a vessel that carries cargo, they can have more cargo, they have more machinery space like with the Galveston Island,” said Webb.
In confirming the engine choice, Gunsten said, “In essence, the hopper dredge is a cargo vessel and it works on a cyclical basis multiple times per day. So the more sand we can carry, the better off we are. Minimizing weight is an important consideration for that type of vessel and it links right into the reduced weight of the engine as well as the lack of the after treatment (weight).”
At the time of the interview in mid-February Galveston Island was in the final stages of build out at Conrad Shipyard. When finished, it is scheduled to enter service at the end of Q2 and most likely join GLDD fleet and operations one of its Gulf of Mexico projects. A sister-ship to Galveston Island is under construction currently at Conrad, with steel cut in late 2022 and expected delivery in 2025.
While dredges are indeed the very definition of ‘Monster Machines’, Gunsten reckons that more than ever software and cloud computing are central to dredging efficiency. “Having a new modern vessel with a modern dredge control and monitoring system (DCMS) allows us to optimize,” he said. “Bridging on that and working into this new cloud-based world, she can broadcast that data and we can access that anywhere in the world, specifically here at our headquarters in Houston, where we plan to set up a data center to look at that information and have our experts analyze that real time. [This means] there's no lag in those optimizations [and we] get the most out of the investment in this new vessel.”
- Galveston Island Main Particulars
Name / Galveston Island
Type / Trailing Suction Hopper Dredge
Capacity / 6,500-cu.-yd.
Shipowner / Great Lakes Dredge & Dock (GLDD)
Shipbuilder / Conrad Shipyard
Main Engines / Wabtec Corporation
2x12V250MDC
2x6L250MDC
Naval Architect / C-Job
Genset Integrator / Cummins
Watch the interview with Chris Gunsten, SVP, Project Services & Fleet Engineering, Great Lakes Dredge & Dock (GLDD) and Patrick Webb, SR Director Sales - Global Marine and Stationary, Wabtec on Maritime Reporter TV.