Future Ships: Picture Perfect
Big data, advanced computers and AI are allowing vessel designers to prepare models that leave essentially nothing to chance.
“Lastly, it may be of considerable importance to form from the draught a block model of the vessel from which a still more accurate judgment may be formed of the fitness and beauty of the body. And should any defect be discovered, farther alterations must still be made, till the draught and the model are perfectly approved of. These different alterations and repeated calculations may appear very tedious, but they will not appear unnecessary to any person at all skilled in the business of construction.”
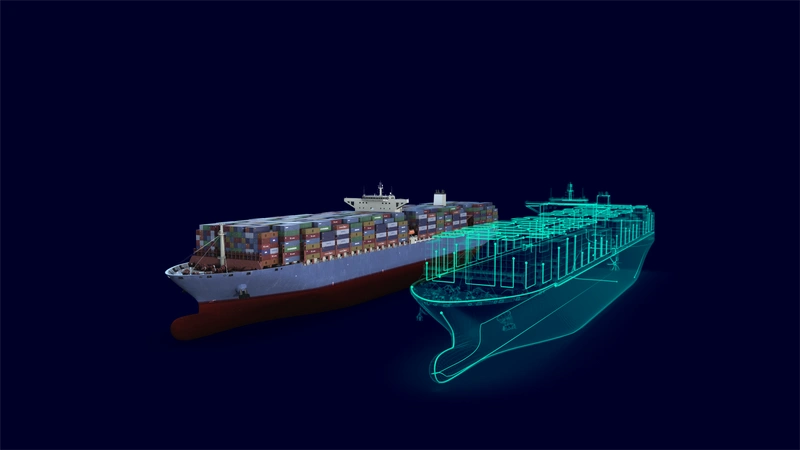
“A Treatise on Ship-Building,” by Frederick Henry DeChapman, Knight of the Royal Order of the Sword, Chief Ship-Builder of the Swedish Navy, 1820. [Text edited slightly.]
Frederick DeChapman’s Treatise includes calculations and algorithms to help predict and match a vessel’s design with its intended mission, e.g., cargo, speed, defense, transport. Consider, for example, the following table to determine the scantling (timber) needed for merchant ships built of oak:
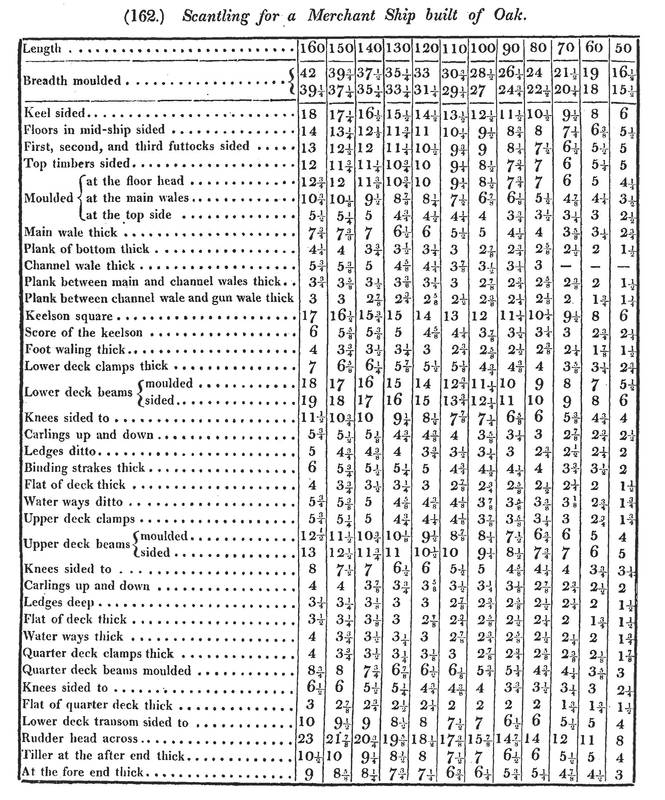
Undoubtedly these tabular references were invaluable for ship designers. Like today, models were critical to advance design. As DeChapman comments the modeling calculations “may appear very tedious” but a model could help assess, before building anything, how a ship would perform in various conditions.
Of course, for something as complex as a ship operating in constantly changing environments, not even the most exact facsimile, prepared by the most skilled modeler, could be expected to uncover every challenge a vessel might encounter. Modeling improved the odds of success, but predictions were hardly guaranteed.
AI: The new modeler
Times have changed. In 2024, that sense of chance, that the real world might rough-up the best thought out plans, is becoming as passe as the slide rule. Big data, advanced computers and AI are allowing vessel designers to prepare models that leave essentially nothing to chance, that a ship will perform with almost 100% certainty in all the conditions it encounters. With AI, what is largely unimaginable at a human scale is now within reach: seemingly every roll and swell of every wave across endless seascapes is now predictable, calculable, and can be offset or otherwise dealt with. In many ways, with ship design today, there are no unknowns.
This sense of certitude comes as a clear message from new design software. Consider, for example, offerings from Siemens Digital Industries Software, a Texas-based business unit of multinational technology and engineering company Siemens that specializes in 3D & 2D Product Lifecycle Management software. In a series of recent webinars addressing 3D simulation and computational fluid dynamics (CFD), the company’s engineers describe expansive, almost all-encompassing digital tools that model and simulate a vessel’s structure, operating systems and hydrodynamics. These modeling results aren’t just theoretical. Siemens’ modeling data is verified by real-world studies. 3D modeling provides more answers more quickly, at less cost and on a real-world basis.
Vessel owners face issues beyond in-house performance demands. Energy and environmental issues, for example, are becoming increasingly stringent. To meet international demands for, say, limits on sulfur emissions or ballast water quality or alt-fuels and engine performance, vessel owners need compliance information before a vessel is launched, not afterwards. Simulation-driven ship design (SDSD) provides the answers needed in advance of purchasing and construction decisions.
In the literature about SDSD design experts comment that ship designers have been slower to adopt this new technology compared to their counterparts in automotive and aeronautical industries. SDSD capabilities accelerate innovation and new tech applications. Older methods impede the design process and check innovative ideas.
Siemens’ Marine Team said they have noted an increase in SDSD use. A big driver, they said, is IMO’s demands for greenhouse gas reductions. “The industry is heavily pushed,” the Team writes, “to revise current procedures and improve processes.” Digital solutions are central for these changes. Consider efforts to use wing sails, Flettner rotors, air lubrication or develop new bow designs. “These solutions require looking at the ship as one system,” the Marine Team comments, “forcing an integrated ship design approach that requires fully integrated tools and processes.”
Other companies are taking advantage of these new capabilities. Designers for America’s Cup vessels, for example, are moving away from in-water testing to SDSD.
NYK Line and Japan Marine United Corporation (JMU), in 2020, introduced a shipbuilding contract that guarantees propulsion performance in actual sea conditions, not just in calm seas, the typical setting for guaranteeing performance. Simulation-driven ship design is integral to these commitments.
Wärtsilä is placing increasing reliance on 3D. In a website blog post, Wartsila writes that the “fidelity of the hydrodynamic vessel models is key to having high confidence in the simulation results.”
Wärtsilä explains that the development of web-based application programming interface (API) capabilities is critical for SDSD. APIs enable different software applications to communicate and to process data transfers between systems, providing answers that would otherwise be very costly, or perhaps impossible, to obtain. Importantly, APIs are web-based, not proprietary. Older modeling systems are labor intensive and repetitive, factors that limit the number of designs that can be analyzed in detail.
Breaking a cycle – the Big Bang Theory
In a 2022 white paper – “Simulation-driven Ship Design” – Siemens describes a “design spiral” to illustrate an older, more traditional procedure for complex industrial design processes. (See illustration.) The spiral proceeds sequentially, work moves from one office team to the next. There is an unavoidable back-and-forth to this multi-team approach. Preliminary power designs, for example, might not square with demands for stability and cost. So, those efforts need to be reworked, likely requiring yet another team meeting. Also, note that the circle starts at the outside, representing an early concept design phase. The circle repeats, moving to the next internal step, as work continues, finally reaching the detailed design phase.
Even if everyone works at top efficiency, Siemens calls the design spiral inefficient, repetitive and rigid, with inherent limits. It’s time-consuming and, even worse, doesn’t allow for true innovation, making it easier to refine an existing design rather than start from scratch and analyze different ways that might improve a vessel’s function.
Simulation-driven ship design combines and makes seamless all of the sequential steps within the design spiral. The Big Bang Theory comes to mind – when everything happened all at once. With SDSD all data is stored and linked. The software creates a master model – a singular point of reference, containing all information, from general arrangement to structural design to marine systems. Individual components can be analyzed by using portions of data from the master model. Teams are no longer siloed since all engineers can access the same model at the same time.
Siemens’ SDSD software can evaluate 500 vessel designs in less than four days, requiring about two hours of computing time per design – that’s computer time, not person-hours.
Recently, Siemens’ Marine Team introduced an “AI Simulation Predictor” to enhance search technology and operate at still greater speeds. This Predictor also allows re-utilization of prior data, providing insights for new products and systems. “For example, the Marine Team writes, “if we already did hull optimization, we can use this data to train our AI model and make it more efficient for each sequential study.”
Critically, users don’t need AI expertise – the technology integrates into existing workflows, accelerating computationally intensive simulations. A user can either finish tasks faster or tackle more simulations within the same timeframe.
Still a disjointed universe
This high-powered wizardry can imply that vessel design now uniformly proceeds as a set of steps that is all-encompassing in efficiency and timeliness, that the “design spiral” can be moved to the maritime museum next to a framed copy of Frederick DeChapman’s scantling table.
In fact, the design universe is disjointed. Even though 3D modeling has been in use for at least 20 years it’s not standardized among ship owners, architecture and engineering companies, shipyards, and, importantly, the classification societies – the organizations which develop and apply technical standards for ship design, construction and surveys. SDSD can replace part of a design spiral, but in the greater design Universe everything has not happened all at once.
The classification society DNV, in a 2023 white paper – “Paving the Way for 3D Model-Based Class Approval” – describes some of these consequences. The author, Ole Christian Astrup, DNV’s Senior Principal Specialist, writes that “lack of standards is a barrier” because of the variety of engineering tools used within the shipbuilding industry. Astrup explains further:
“This heterogeneity has created both technical and business challenges. Data integrity across the applications and systems that author and consume engineering data is problematic. Point-to-point integration between systems is often so complex and costly that organizations opt for manual data re-entry when faced with program budget and schedule constraints. This decision has a lasting impact on information quality, supplier management, manufacturing integration, and in-service support.”
Note the reference to “manual data reentry;” brings to mind – in 2024 – copying fractions from DeChapman’s scantling table as well as his comments that modeling calculations “may appear very tedious.”
In an interview Astrup said that manual drafting, say, for a cruise ship, can take up to 5,000 person-hours.
Astrup’s paper describes an effort by DNV, starting in 2016, to standardize 3D format and process, to eventually replace 2D drawings with 3D modeling. The result was the development of the ‘Open Class 3D Exchange standard’, or OCX. DNV was joined in this effort by other classification societies and software companies, including Siemens. The group is now called the OCX Consortium. Its goal is to complete the 3D standardization and push for adoption across maritime sectors. Potential benefits are vast – like going from a rotary phone to an iPhone.
Successful projects emerging
The OCX effort is moving forward. Importantly, in November Bureau Veritas (BV), the Shanghai Merchant Ship Design & Research Institute (SDARI) and NAPA completed the first phase of a joint development project (JDP) to enable 3D model-based approvals for the classification of ships. The report tells that the “project validated the feasibility of 3D model-based approvals rather than requiring multiple conversions to 2D drawings, which is the traditional process.” The project goal was to use the open file format to boost design efficiency and “save time and costs and improve accuracy and communication between all parties.”
BV was asked about the SDARI project, about some of the key learnings. Olivier Degrand is Director of the Business Ownership for Digital Solutions for BV. In an email he said the project confirmed workflow (see diagram) and validated exchange data between the shipyard and BV using the OCX format. Degrand cited the following benefits:
- 2D drawings were not necessary;
- Shipyard workload was reduced;
- Design verification was quicker; and,
- Collaboration was enhanced.
Critically, Degrand said that all design data are part of a centralized 3D model, which he called “one single source of truth” because “all actors can connect at the same time to the 3D model to exchange (information) directly.”
The American Bureau of Shipping (ABS) is listed as an “Observer” member of the OCX Consortium. Patrick Ryan is ABS Senior VP and Chief Technology Officer. Ryan said that ABS actively supports the OCX Consortium and “endorses the work of this group.” He said it has its “place in the landscape of digital transformation but it is one piece of a larger whole.”
Ryan said a top concern is value of the OCX models and tools in ship production, a process that still requires unique CAD attributes that differ from shipyard to shipyard and differ from what Class societies require. “Driving shipyards into a standard they must maintain may constrain their (overall digital) transformation.”
Ryan said it’s ABS’ position that shipyards “should communicate with downstream stakeholders in whatever format is most efficient for them — this will drive the most efficiency through the whole ship construction value chain — and so we accept many formats for digital review, of which OCX is only one of them. OCX certainly can be used with ABS if that is in alignment with the strategy of the shipyards. It has its place and will evolve and become more useful as time goes on.”