In Focus: Talking Workboat Safety with AWO's Brian Bailey
Brian Bailey, Director of Safety and Environmental Stewardship for the American Waterways Operators (AWO), was recently named a 2020 Rising Star of Safety by the National Safety Council (NSC), a nonprofit public service organization promoting health and safety in the U.S. Marine News spoke with Bailey about workboat safety and the AWO’s mission to protect industry workers, assets and the environment.
Please tell us a bit about yourself and your role at AWO.
I’ve been with The American Waterways Operators as its Director of Safety & Environmental Stewardship since 2016, and lead continuous improvement efforts to promote safety, security and environmental stewardship the tugboat, towboat and barge industry. Specifically, I administer members’ compliance with AWO’s requirement that carrier members maintain third-party audited compliance with a safety management system (SMS), specifically the U.S. Coast Guard-accepted Responsible Carrier Program; the Safety Statistics Reporting Program, a safety data point collection repository; and, the activities of the association’s safety committees and subsidiary groups including the Tankering & Barge Operations Subcommittee. I have more than 10 years specializing in the successful leadership and management of organizations and programs. I’m originally from the Baltimore metropolitan area and am a graduate of the University of Maryland, Baltimore County.
Why is it important for industry stakeholders to come together on safety issues? And best case scenario, what can be achieved through discussions such as those arranged by AWO and other groups?
I believe in safety evangelism. And, the importance of convening the broader towing industry community to learn about and engage on safety issues is more critical than ever. Each and every employee in the towing industry knows safety is important. They all want to work in a safe and healthy atmosphere. Each and every AWO member company believes it is their responsibility to look after employees – whether they’re shoreside or afloat. Real change can happen when we sit down together and brainstorm, attempting to develop real, tangible safety solutions to make sure that everyone returns home from work the same way they left.
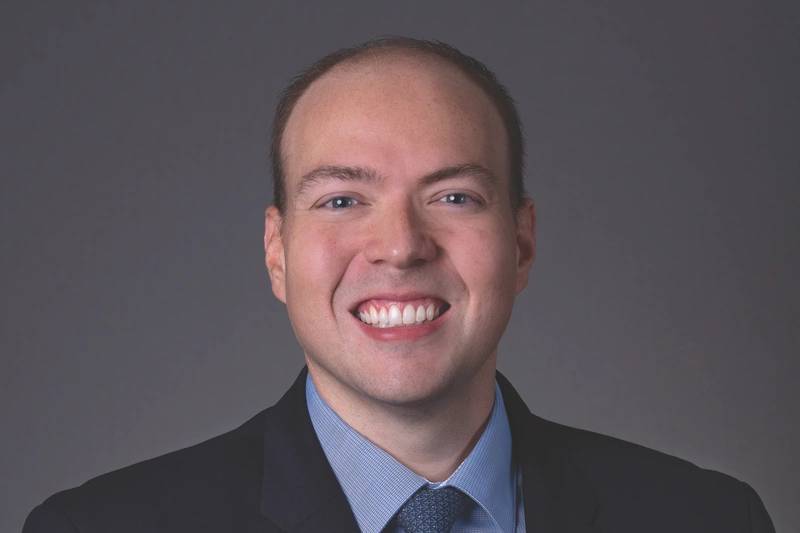
To give an example, the Tankering & Barge Operations Subcommittee, a subsidiary of the Interregion and Coastal Safety Committees, has identified the need for safe and reliable means of access/egress at the vessel-to-facility interface. The group noted the lack of regulations addressing access/egress between ship and shore leads to a haphazard system that puts individuals at risk of injury or even death. They brought together a large group of stakeholders, did some data collecting, reviewed the most commonly used systems for access/egress, delved into examples of safety risks that tankermen and others encounter, designed a work process to mitigate these risks, and lastly provided recommendations to close access/egress safety gaps over time. All this was published in a memo entitled “Mitigating Access/Egress Risks at the Vessel-to-Facility Interface.”
Other than COVID-19 issues that have dominated safety talk this year, what do you see as the top safety issues frequently discussed among AWO members?
Fall overboard prevention continues to be a top issue and safety priority. And, as an industry, we must do all we can to fully understand and promote the contributors to falls overboard, which can sometimes lead to fatalities, the human factors that play a role, and the preventative measures that can be taken by the company and the mariner to reduce that mariner’s risk exposure. AWO, in reviewing its U.S. Coast Guard and AWO Safety Partnership data in February 2019, noticed that nearly half of the towing vessel crew fatalities since 2010 resulted from falls overboard incidents, despite a 2012 Quality Action Team report on Reducing Fall-Overboard Crew Fatalities produced by the Partnership. In response, AWO constituted the Permanent Subcommittee on Operational Crew Fatalities to continue studying this issue of the industry’s operational crew fatalities, including individual incidents and causal factors, paying particular attention to the problem of falls overboard incidents. One of the best ways to prevent incidences such as falls is an effective and robust culture of safety. To AWO this means that companies must utilize an effective safety management system which reduces the risk of incidents, injuries and fatalities through ongoing data-driven measurements designed through continuous improvement in safety performance. Safety is everyone’s responsibility, and safety culture must include components such as visible, felt leadership; effective training; open, transparent communication; employee engagement; and training. However, even the best safety culture isn’t 100% fool and fail proof.
Overall, how would you rate the industry’s response to COVID-19 from a safety perspective?
While our industry, like all Americans, has been challenged by this global health crisis in profound ways, the domestic maritime supply chain has proven resilient in the face of COVID-19. The men and women of the tugboat, towboat and barge industry have played a key role in keeping our nation’s economy afloat, remaining open for business and continuing to move essential cargoes. Tugboat, towboat and barge companies have been able to maintain business continuity in large part because employers recognized early on that mariners are the lynchpin of their operations and protecting crewmember health and safety is key to keeping vessels moving and commerce flowing. The industry’s extensive experience with contingency planning, safety management systems and incident command structures has served it well in managing the health, safety and operational challenges posed by the pandemic. The result of these concerted and cooperative efforts has been to keep COVID-19 infections among the mariner workforce to a minimum – a win-win for health and safety and for the resilience of the maritime supply chain. To maintain this situation, it will be extremely important for employers, mariners and regulators to remain vigilant and not relax prematurely the prevention policies and social distancing procedures that have proven successful in keeping vessels largely virus-free.
From your point of view, what are some of the top ways Subchapter M has affected industry safety?
Subchapter M has incentivized more towing companies than ever before to implement safety management systems. The experience of AWO members with the Responsible Carrier Program, which was accepted by the Coast Guard under 46 CFR §138.225(b) as an existing safety management system, has demonstrated that implementing a safety management system has produced quantifiable benefits in the form of fewer vessel incidents and personal injuries. That is why AWO continues to believe that the implementation of a safety management system is in and of itself the best way to promote continuous compliance. The purpose of a safety management system is to drive continuous improvement in safety performance, and its pillars—which are reflected in the TSMS requirements of Subchapter M—include procedures for verifying vessel compliance, assessing performance, identifying and correcting non-conformities, and applying lessons learned. We can already see from the data compiled by the Coast Guard that towing vessels using the TSMS option have far fewer deficiencies and detentions that towing vessels using the Coast Guard option.