Almacam Helps Cut Shipyard Waste, by Design
Almacam is a leader in nesting-CAM software for shipyards. Philippe Rouzeau, Manager of the Shipyard Team, Almacam, explains how it solutions can help shipyards shave production costs and increase efficiency.
Almacam is a 45-year-old, employee-owned company created by researchers that were mono-focused on developing nesting algorithms in a laboratory of Grenoble University, France, aiming to bring this nesting algorithm tech to the industry.
According to Rouzeau, it is the world's only independent CAD-CAM software publisher offering CAM solutions across industries, including aeronautics, agricultural equipment, steel construction, mechanical welding and, of course, shipbuilding and offshore construction.
Today the Alma Group has a nearly $20 million turnover, supporting 170 crew members and eight subsidiaries in France, Italia, Germany, Spain, Singapore, China, Brazil and the U.S. It works with 20 resellers and partners globally, with approximately 30,000 product licenses globally, a total which includes equipping 40 shipyards, with shipbuilding cumulatively representing approximately 20% of its overall market.
“I think the shipbuilding market is a bit conservative regarding modern technologies, but this can be easily explained,” said Rouzeau. “First, the shipyard must keep and continue to use its CAM solution for the ships, or series of ships, that has been already built, sometimes for tens of years, for maintenance or traceability constraints. They cannot afford to use two CAD-CAM solutions for the same project. As a result, they adopt a new CAD-CAM solution when they launch a new project, and that does not happen every day.”
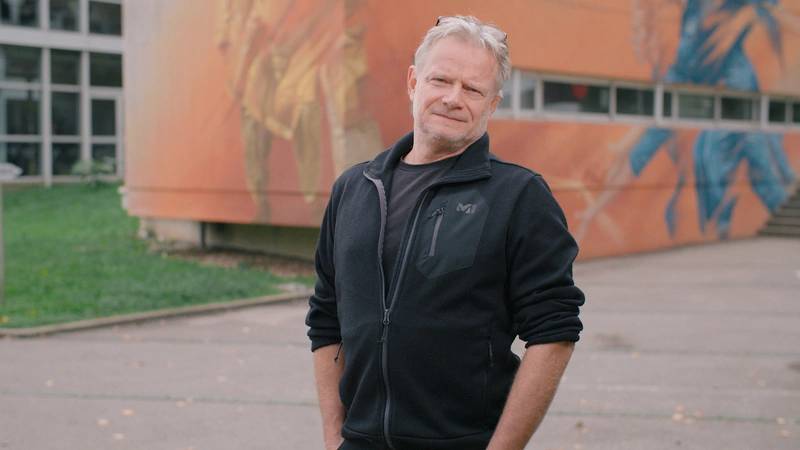
– Philippe Rouzeau, Manager of the Shipyard Team, Almacam
But the main reason is that the adoption of the new CAD-CAM solution, however effective it may be, impacts a lot of people in the organization of a shipyard. “So the IT department is involved because he has to integrate with, or help, our CAD-CAM system inside their IT environment. The design, meaning the CAD department, is involved because they are providing data for the CAM. The methods department is involved for the technical specificities linked to naval domain. And the workshops are impacted for the control of the cutting machine,” said Rouzeau. “It is not enough to propose an innovative solution, even reducing material cost or controlling efficiently is the cutting machines. It is necessary to work with all these guys from all these departments, in order to integrate the CAM solution into the overall environment of the shipyard. And integration means communication with the different design or management systems, such like MRP, MES, or CAD system. And it means, also, to control, in the most automated way possible, the specific machine equipping the shipyard.”
Rouzeau started working in more than 30 years ago, starting with Chantiers de l'Atlantique, which was Alma’s first shipyard customer as they were looking for a nesting engine to reduce their material cost. “The shipyard market has always been a niche but very important market for Alma,” said Rouzeau. “We have deployed our CAM solution into many big shipbuilders,” including Fincantieri in Italy, Meyer Werft in Germany, Cochin Shipyard and Larsen & Toubro in India, and Bath Iron Works in U.S.
Today Rouzeau focuses on managing complex projects in the shipyard domain “from A-to-Z,” starting early in the pre-sale stage to the final deployment and the start of production in the yard. “My role is to help shipyards to digitalize their process, and to integrate our Almacam solution in their environment.”
Show Me the $
There is not a manufacturer in existence that shouldn’t have ‘cutting material cost’ as a Top 2 agenda item, as controlling material cost and profitability walk hand-in-hand. Estimating actual material and cost saved is not easy premised on the fact that no two shipyards operate the same, but Rouzeau did offer guidance.
“The main gain a shipyard can expect by using a powerful CAM solution is the reduction of material cost, using parts coming out of a 1-in. (20mm) block as an example.
“For such a thickness, we may have, for one block, approximately 400 to 500 different parts with complex shapes to nest. This can lead to approximately 20 nesting in a standard sheet format of 10 x 4m,” said Rouzeau. “We did several benchmark studies which showed that we can save one or two sheets among the 20, so it means a reduction of waste of approximately 10%. We cannot expect such wins on all thicknesses because the number of parts to nest can be much lower for different thickness. But if we take a 4% average wins ratio for a complete block, we can make a projection on a complete cruise vessel of 30,000 tons, for example. With a material cost of approximately $800 per ton, we can calculate a win in material cost between $900,000-$1 million,” meaning the shipyard could effectively achieve a return on investment in a matter of months.
While material savings are tangible, additional benefits using optimization algorithms such as cutting-pass calculations can reduce machining time.
“In addition, most of the time our solution is fully automated and can run in full batch mode,” said Rouzeau. “So the programming time is also greatly reduced, and the risk of error, too. These are smaller than material wins, but they have to be considered in the choice of a new CAM solution.”
Watch the full interview with Philippe Rouzeau, Manager of the Shipyard Team, Almacam on Maritime Reporter TV: